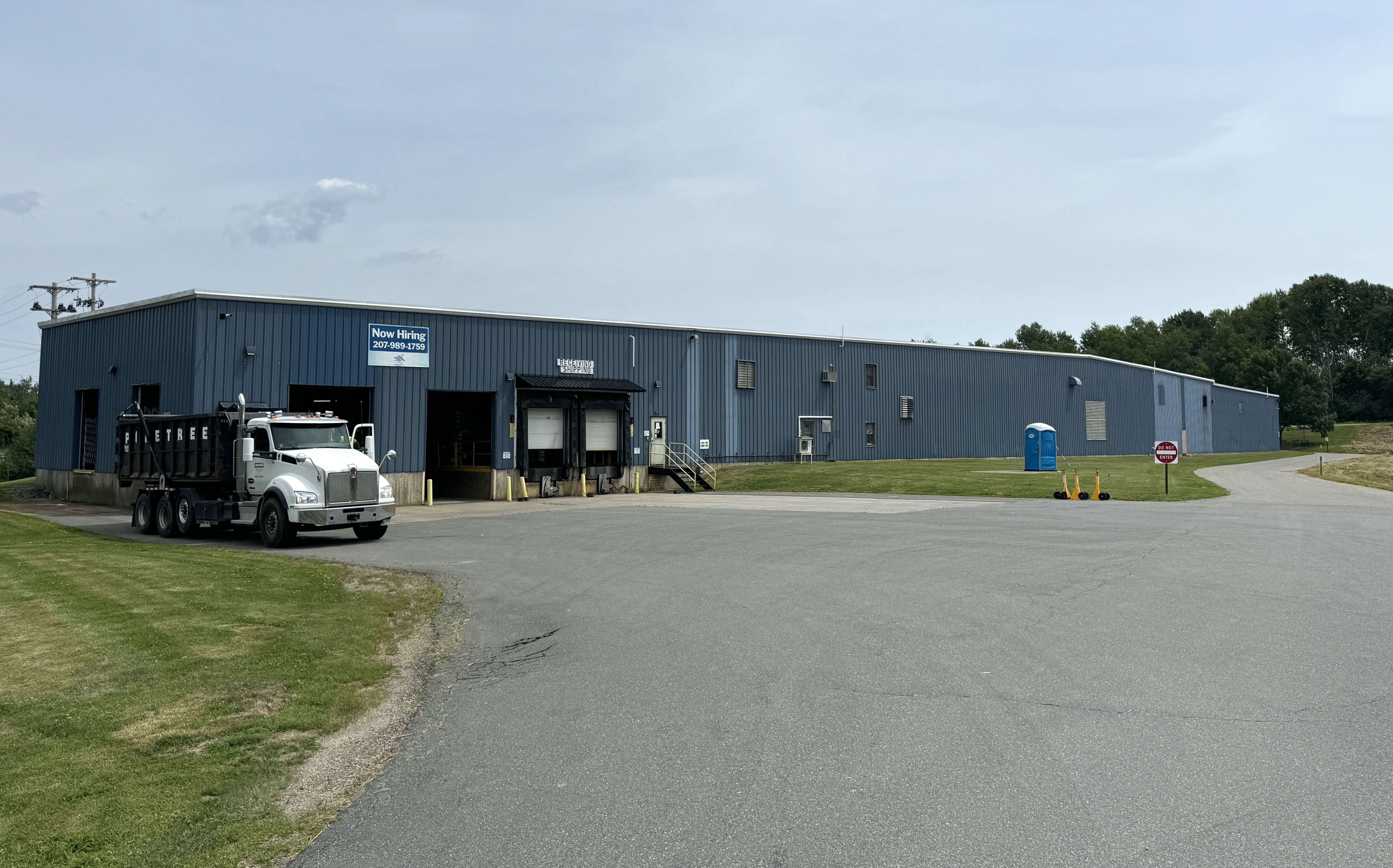
Please do not leave this page until complete. This can take a few moments.
A Brewer manufacturer that turns out steering and suspension components for three of the world's major automakers is spending $15 million on equipment that will enhance the plant's automation, efficiency and inspection systems
“This bring us into the future,” Daryl Boyington, equipment procurement engineer and designer for Somic America Inc., told Mainebiz.
The company spent $7 million on specialized equipment last year. An additional $8 investment is underway this year and next.
Somic America, at 6 Baker Blvd., is a subsidiary of Somic Ishikawa, which is based in Hamamatsu, Japan, and has been in business for over 100 years.
Somic Ishikawa specializes in the design, development and manufacturing of automotive components and has factories in seven countries. Somic America is comprised of two manufacturing facilities, in Brewer and in Wytheville, Va., with administrative offices and both locations.
Somic America specializes in the manufacturing of steering and suspension components, including ball joints, tie rods, stabilizers and dampers, for Toyota, Honda and Subaru in their North American and South American automotive markets.
Somic America’s origin dates back 35 years. It initially started under the name Brewer Automotive Components in 1989 as a joint venture of Somic Ishikawa and Lemforder, a German automotive components maker, according to a company history.
In 2010, Brewer Automotive Components merged with Wytheville Technologies Inc., a similar company established in Wytheville, Va., in 2000. The merged companies became Somic America Inc.
The Somic America engineering team designs and develops custom components and systems in-house with 3D printers, in plastics currently, and soon to be capable in metals. Additive manufacturing technology is utilized to create custom fixtures to make the parts. “Fixtures” are tools used within machines for operations such as the assembly of the parts that make up the finished assemblies for ball joints, toe links and stabilizers into final assemblies to ship to customers.
Nearly every machine on the manufacturing floor uses at least one robot designed to provide precision accuracy, speed, consistency and efficiency.
The high-tech machine cells come from all over the world, and all have built-in quality measurements and checks. Integrated quality checks are important to the process because many of the parts produced are safety critical in their function within the vehicles that they are assembled into, such as ball joints and toe links, said Boyington.
The parts made by the Brewer and Virginia plants are found in many Toyotas in North America, as well as many Subarus and Hondas, said Boyington.
This year, Toyota Motor North America Inc. awarded Somic America a Superior Quality Performance Award and an Excellent Launch Performance Award for components of the Toyota Grand Highlander/Lexus TX car models.
Production in Brewer last year was 7.8 million outbound finished goods, including 3.2 million ball joints and 2.25 million tie rods, said Boyington.
In 2023, the Brewer plant brought in a ball joint assembly system relocated from the Virginia plant, in order to support Toyota’s growth in battery electric vehicles for suspension ball joint machining and assembly. Investment in plant infrastructure and new equipment, which also included the addition of an automated lathe, was close to $7 million.
The Brewer plant has just over 100 employees across three shifts. Its revenue for 2023 was $60 million.
The Virginia plant has 371 employees. There are another five employees in a small Detroit location, which is expected to expand.
The goal of new equipment coming to Brewer is to automate many of the plant’s manual operations and align the system of producing parts using the Lean and Six Sigma manufacturing approaches, both of which aim to optimize efficiency and minimize waste, said Boyington.
For example, employees previously manually loaded raw material into a ball joint machining system. New automated feeders and three robots now load the materials in an optimized manner. The system can be run by one operator.
The goal is to transition to where one technical operator runs several automated machines that are part of a unified system, as compared with several operators needed to load and operate machines.
Cameras and other quality control components allow parts to be inspected as they go through the system.
“These parts are safety critical,” said Boyington. “So we need checks in place to be sure that what we’re producing is safe and meets design specifications.”
Several more component-machining systems are due this year and next. That includes a $4 million ball joint machining center with automated loading, unloading and measuring capabilities and semi-autonomous operating equipment — all built into a single system that carries out all of the steps.
Human operators will still be needed to bring raw material to the system, change the tooling when necessary, and take away finished goods. But the consolidated system compares with previous operations that were carried out by a number of machines, with human operators needed to move production along from machine to machine.
Also on the books is a tie rod assembly piece of equipment, which combines many steps that up to now have been done separately. A human operator will still be in place to carry out manual inspection of parts coming off the system, in order to verify that all specifications were carried out correctly before the parts are packed. The machine will perform pre-assembly, final assembly and parts-tempering — a heat treatment process that improves a material’s properties.
“Up to now, those were done in separate operations,” said Boyington.
The system will have larger hoppers that’s expected to allow for four continuous hours of operation, compared with, at most, 15 minutes allowed by the smaller hoppers used on the plant’s machines to date.
The machines are coming to Brewer largely from Japan and Europe.
The plans is aiming to improve efficiency and quality control, with a gradual production uptick as the new machines come in, said Boyington. The number of employees will remain about the same, he said.
Somic America has several programs to recruit and retain employees.
That includes attending career fairs at the University of Maine with an eye out for business and engineering students and being active on UMaine’s job boards to hire student interns.
Somic has a training program and onboarding process that takes staff from instruction to implementation of processes such as managing the machines’ computers, performing tool changes and conducting quality checks, with oversight and guidance.
The company incorporates a Japanese philosophy called “kaizen,” which is based on the concept of little changes compounding to make large change. That approach empowers employees to identify ways to improve and streamline processes, according to the company’s website.
Benefits include medical, dental, vision, disability and lift insurance; an employee assistance program, parental leave, sick time, vacation time, incentive bonuses and quarterly luncheons.
“Our team leaders wanted to emphasize that Somic America's investment in quality people is just as important as investment in new technology for the future,” said Kyle Flynn, the company’s U.S. marketing specialist.
Amazing!!
1 Comments