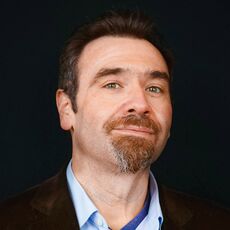
Please do not leave this page until complete. This can take a few moments.
A new forest product sector in Maine is heating up as startup companies establish facilities to turn forest residuals into a versatile high-value product called biochar.
Biochar is the solid material obtained from the thermochemical conversion of biomass in an oxygen-limited environment.
The conversion process, called pyrolysis, can use softwoods and hardwoods, which are in equal proportion in Maine’s forests, and can be the lower-value forest residues from typical harvesting operations, from low-quality pulp chips and from pre-commercial thinning, says Shane O’Neill, forest industry business development manager at the University of Maine’s School of Forest Resources.
Uses include agriculture applications such as soil amendments and animal bedding, environmental remediation, stormwater management, and as an additive to cement and asphalt. Some high-quality biochars can also be used in environmental remediation of heavy metals and PFAS.
Carbon sequestration is an added benefit as biochar permanently locks carbon which would otherwise be reintroduced to the atmosphere through combustion or decomposition.
In Maine, Clean Maine Carbon recently started its facility in Greenville and Standard Biocarbon expects to start operations in Enfield.
Other companies are evaluating Maine for potential locations, says O’Neill.
“With the decline of paper production in Maine, the state’s forests could provide an estimated eight to 10 million green tons annually to the manufacture of biochar, effectively replacing the lost consumption from the shuttered papermills,” says O’Neill.
Those harvest levels would result in approximately 1.2 to 2 million tons of biochar.
The University of Maine is involved in several areas of biochar research, including improving crop yields in Maine blueberries, PFAS and other toxin remediation, and characterizing the pyrolysis processing and species variables effects on biochar properties.
In 2017, Clean Maine Carbon purchased the Greenville Steam Biomass facility in the Piscataquis County town of Greenville.
Starting operations in the mid-1980s, Greenville Biomass has been idle for a decade or more.
Clean Maine Carbon’s original vision was two-pronged: provide clean energy to northern Maine using low-value, discarded woody mass and create biochar as a valuable byproduct of energy production.
The energy-production side of the equation was stalled by the state’s regulatory process.
But plans for producing biochar advanced and the facility began operation in July.
To date, Clean Maine Carbon has invested over $4 million in the project, financed by 10 investors and Skowhegan Savings Bank. There are six employees and more hiring is anticipated as production increases.
The process uses pyrolysis rotating drum technology — a rotary kiln system — made by BioMass Energy Techniques Inc. in Versailles, Mo. Additional equipment includes feed bins converted from heavy-duty farm equipment and a front-end loader.
“Think of a big barrel,” says the company’s president, Patrick Jones, describing the kiln. “It operates at a very high temperature. Waste wood goes in and it’s pyrolized within a starved-oxygen atmosphere that works the volatile organic compounds out of the wood and leaves behind mostly carbon. You end up with biochar.”
The plant is so far receiving about a truckload of waste wood per day from a couple of area mills. About 225 cubic yards of biochar in total have been produced in the plant’s first weeks. Ultimately, production capacity is expected to be 15 to 25 cubic yards per day, or four to six tons.
Jones says biochar is a high-value product with applications in agriculture, construction, and water and air remediation. In general, markets are in various stages of development to integrate biochar as a green amendment with concrete and asphalt, as a farm feed additive, and to remediate water contamination.
Clean Maine Carbon has identified potential customers. “The uses are quite wide,” says Jones. “Agriculture is the largest potential use and it’s used a lot on the West Coast.”
For agricultural purposes, biochar is “charged” with organic material such as worm castings, compost or cow manure. “It’s like a microbe condominium program,” says Jones.
Introducing its product to the market, Clean Maine Carbon is so far selling biochar at low cost or even giving it away.
“We’re getting it out there,” Jones says. “That’s good for us and for other biochar manufacturers.”
The market could be large, he says.
“The other side is that it reduces waste wood in the forest and provides employment within the forest products industry,” he continues. “This could be another revenue stream for wood producers.”
The marketing plan includes networking with organizations such as the Maine Farm Bureau and the Maine Organic Farmers and Gardeners Association.
“We try to meet people face to face,” says Jones. “We’re working with the USDA to access programs to incentivize farms to utilize biochar, and with direct customer contacts for large end-users.”
For Greenville, the facility’s revitalization is great for the community, says Town Manager Mike Roy.
“The $4 million investment from Clean Maine Carbon is awesome and it shows commitment to what they’re doing,” says Roy.
Says Jones, “We want to go full speed ahead. We want to be part of the community.”
In the Penobscot County town of Enfield, Standard Biocarbon Corp. expects to open late this year or early 2024, says Frederick Horton, CEO, who founded the company with his brother Tom in 2020.
The biochar plant is co-located at the Pleasant River Sawmill, at 542 Hammett Road in Enfield, where the site offers a reliable supply of clean, high-quality feedstock in the form of mill residuals. Chris and Jason Brochu, co-presidents of Pleasant River Lumber, have provided invaluable support and assistance to the establishment of the operation.
SBC, headquartered in Portland, will utilize “pins and fines” from the state-of-the-art low-diameter spruce fir mill, creating a new outlet for the low-value byproduct.
The investment to date is nearly $10 million. Funding was provided by loans, grants and tax credits from Coastal Enterprises Inc., Finance Authority of Maine, Maine Technology Institute the U.S. Department of Agriculture and the U.S. Forest Service.
Additional funding was provided by a carbon credit streaming agreement and associated royalty agreement with Toronto-based Carbon Streaming Corp.
The plant will use two high-tech German-made pyrolizers which can precisely control reaction temperature and flow rate to produce consistent high-quality biochar. The pyrolizers, are housed in a new 50-by-125-foot building supported by a feed system, chip drying and sizing technology and a bagging system. The technology is designed to produce precision biochar suitable for high-value uses, such as the remediation of PFAS contaminants and heavy metals in soil and water.
Horton notes the technology, operating at 600-plus degrees Celsius, or over 1,000 degrees Fahrenheit, requires feedstock to be properly prepared in terms of attributes such as size distribution and moisture content. The high temperature and low oxygen, he says, results in a product that’s consistent with over 90% carbon content by weight, very low ash and near neutral PH.
The feed system is made by Indianapolis-based BE&E, or Biomass Engineering & Equipment.
SBC’s plant will operate 24/7 and produce about 160 tons, or 950 cubic yards, monthly.
SBC will produce carbon removal credits certified by Puro.earth sold to emerging private carbon-credit markets, which offer corporations and individuals the opportunity to “buy back” their emissions.
Horton says agriculture is the best-established market for the product.
“Our near-term market is agricultural use in Maine and focusing on animal husbandry for bedding and field applications as well as supplying the bagged soils industry,” Horton says.
The company is also eyeing environmental remediation and stormwater management, along with other emerging uses in cement, pavement and advanced materials such as graphene and electrodes.
“Our strategy is to approach the biochar market with quality and consistency over quantity,” he says. “We believe that the really deep demand will require biochar at that level of purity.”
The company is working with potential customers in Maine and beyond, and with the University of Maine, which have indicated interest in taking small amounts of biochar for commercial and academic research.
“We’ve been talking with farmers of high-value crops and with dairy farmers about uses in bedded pack and in feed,” says Horton. “We’re also working with environmental remediation contractors who have been using biochar to treat PFAS and heavy metals contamination in soil and water. Related to that, we’re talking with companies that make media for high-volume filtration applications for either post processed wastewater or contaminated well water. We also think there’s an opportunity in specialty materials like polymers and concrete mixes that can lower the carbon footprint of those materials.”
Horton continues, “It’s a super exciting time. We look forward to continuing to engage with our natural users, to developing relationships and partnerships where we can supply them with this carbon negative, highly versatile material that they can use to make other high-value products like soils, like environmental remediation, like carbon-negative products. We hope biochar can become a catalyst to drive other industries in Maine.”
0 Comments