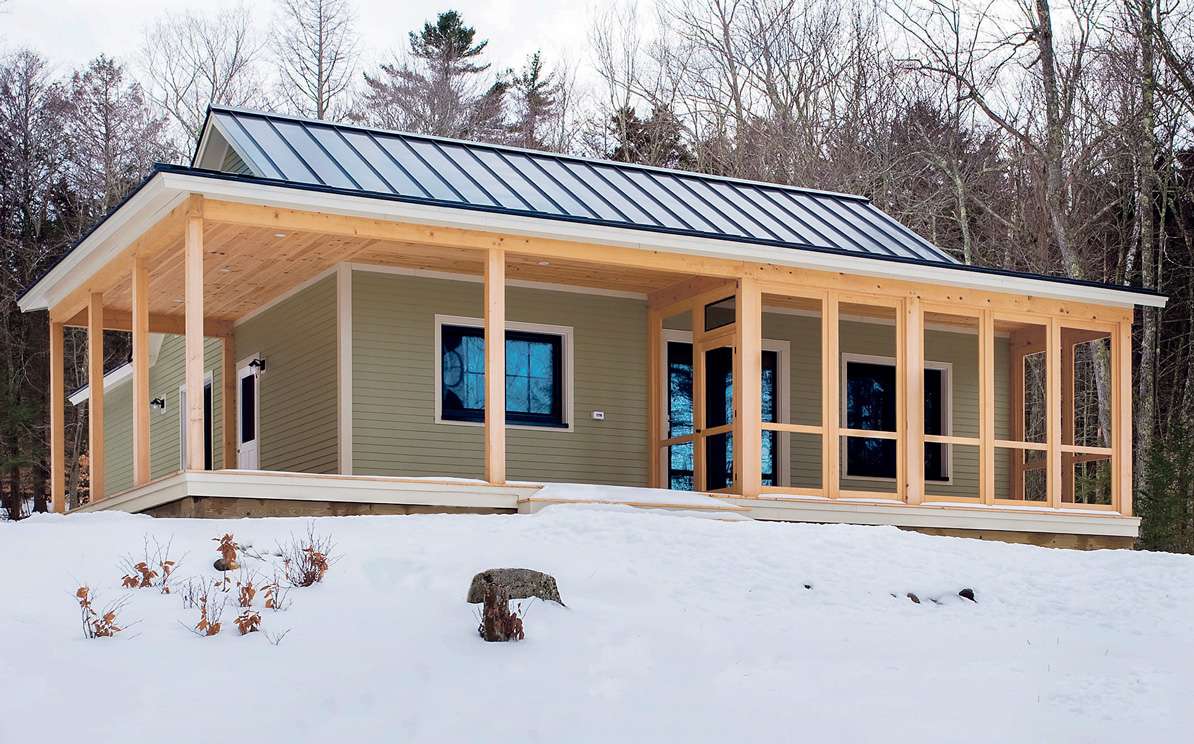
Please do not leave this page until complete. This can take a few moments.
In 2014, when Chris Corson founded his passive-house design and construction company, Ecocor High Performance Buildings, his customers were largely scientists.
“Probably the first 10 passive houses I built were for people in some sort of field like electrical engineers or computer science,” he says. “They were people who, by the nature of their training, understood the benefits of passive house right out of the gate.”
Corson, as one of the first passive house builders in Maine, saw potential for a broader market. His company is the first certified manufacturer of passive house components outside of Europe. It produces wall and roof panels for minimum-waste, saving time on the job site with pre-assembly. Ecocor uses natural materials with zero volatile organic compounds and sources wood from within 200 miles.
Corson’s persistence paid off. Now he’s doing several projects at a time, in Maine and beyond, with commissions coming from as far as the West Coast. Initially focusing on single-family residential, his market is growing to multi-family residential and he plans to expand to larger commercial projects with the development of customizable panels.
Interest in the construction technique and its energy-saving potential has broadened significantly over the years, he says.
“We’ve seen a steep increase in passive house projects between 2010 and 2019 in the United States,” says Corson. “It continues to grow.”
Construction of energy-saving structures is also gaining ground in Maine. At one time, the concepts behind “passive house” and “high-performance” construction had the attention mainly of energy-minded consumers. Today, there’s general awareness of the terms, which indicate precise construction standards to minimize energy use. Interest is pushed by factors like proven outcomes coupled with growing concern about climate change and the potential to reduce carbon footprint.
“Ten years ago there were three or four of us who were serious about it,” says Brenan Black, co-owner of Black Brothers Builders in Rockport. “In the first five years, no one knew what we were talking about. We had to take time to tell people, step-by-step, what we were doing and why. People are much more aware now.”
Bob Muller, the owner of Landicity Builders in Brunswick, recounts recent interest in Brunswick “eco-conservation” residential subdivision Douglas Ridge. There, he’s building high-performance homes, using energy-efficient, air-sealed components manufactured by Unity Homes of Walpole, N.H. Douglas Ridge homes range from $420,000 for a two-bedroom model to $585,000 for a three-bedroom, 2,200-square-foot home. An open house for a home still under construction drew 50 people.
“That’s the level of interest,” Muller says. “And that was only two hours on a Sunday. When we held another open house, after we finished it, we had another 50 people. We had a contract within five days.”
But there’s still a long way to go.
Asked how much demand he’s seeing in Maine, Corson replies, “Not enough.” He continues, “There’s little thought given to the building envelope, quality of the windows, level of thermal insulation, mechanical ventilation, durability and longevity of the structure, and air-tightness.”
Passive house construction costs about 10% more than standard construction. But the proponents say the difference is more than covered by savings in energy costs.
“We tend to say, on a small scale like a house, that if people assume approximately a 7% to 10% increase in construction costs, they’re going to realize an 80% to 90% reduction in operation costs,” says Timothy Lock, a management partner with Belfast-based OPAL (the architectural division of Belfast-based GO Logic), lead designer for College of the Atlantic’s planned passive-house Center for Human Ecology in Bar Harbor. “Typically, the return on that extra 10% in investment is in the six- to eight-year range. It’s a pretty quick return because you’re saving so much on energy.”
The first passive house in the U.S. was built in 2003, according to the nonprofit Passive House Institute US. Standards are based on climate-specific comfort and performance criteria — an estimated 60% to 85% more efficient than conventional construction, the institute says.
In 2011, GO Logic built Maine’s first passive construction, a dorm at Unity College. The technique has mainly been adopted for single-family homes, but there’s a growing number of commercial projects, like Wright-Ryan Construction’s Village Centre, a 48-unit development in Brewer.
Passive construction standards are increasingly well-known in Maine as a highly insulated structure with airtight envelopes, ventilation to provide a steady supply of fresh air, high-performance, triple-glazed windows and orientation of the structure to maximize solar gain.
The concept is relatively simple, with some differences from conventional framing.
Village Centre is wood-framed, which is conventional for housing, but the walls can accommodate 12 inches of cellulose insulation. Early on, materials needed to provide an airtight envelope, like air-seal membranes, were mainly sourced from manufacturers in Europe, where passive construction is a longstanding practice, says Steven Konstantino, owner of Performance Building Supply in Portland.
Today, “almost any builder knows about the value of air sealing a structure. In 2002, nobody talked about it,” he says.
“A lot of the materials are becoming standardized,” says Reggie Lebel, president of Emerald Builders in Bowdoinham, builders of net-zero and passive homes. Emerald’s practices includes frequent blower door tests throughout construction and use of cellulose insulation. In 2006, Lebel says, he was trying to educate clients about ideas like adding more insulation. Now, he says, “Homeowners are coming to us with specifications. The public is much more educated and much more on board.”
There’s education on the construction side, too.
“You want to make sure everyone on your team understands what you’re doing,” says Jesper Kruse, owner of Maine Passive House in Bethel. “The big thing is air-tightness. You have to go through the steps to make sure you’re maintaining the air barrier. Then there’s all the subcontractors. They can’t just drill a hole willy-nilly.”
Customers seeking lower energy costs and lower carbon emissions are driving the sector’s growth.
The carbon footprint of construction, Lebel explains, includes materials extraction, transportation and processing, and energy to run the building. The ultimate goal, he says, is to create “carbon sequestering” buildings. Carbon sequestering components include wood and other plants that absorb carbon while alive. An analysis of the amount of carbon sequestered by buildings is based on the processes that turned the tree into a building component.
“That’s why we as a company and other people are looking at the whole life cycle of wood,” says John Deans, Emerald’s sustainability expert. “Wood stores carbon. But if the way the wood is harvested reduces the forest’s ability to store carbon, it diminishes the value of that carbon-sequestering material.”
“We have this amazing opportunity in Maine to drive the conversation on sustainability,” says Lock, who is also chair of the American Institute of Architects/Maine’s committee on the environment. “Maine has a unique and direct relationship with its environment and resources. It costs a lot of money to pay for heat in Maine in the winter. You feel that not just when you walk outside, but in your wallet.”
Kruse adds: “More and more people are waking up to the fact that climate change is happening and we’re going to get screwed and something has to change, and if you decide to build a new house it really ought to be something that’s up to par with the reality of the world we live in.”
0 Comments