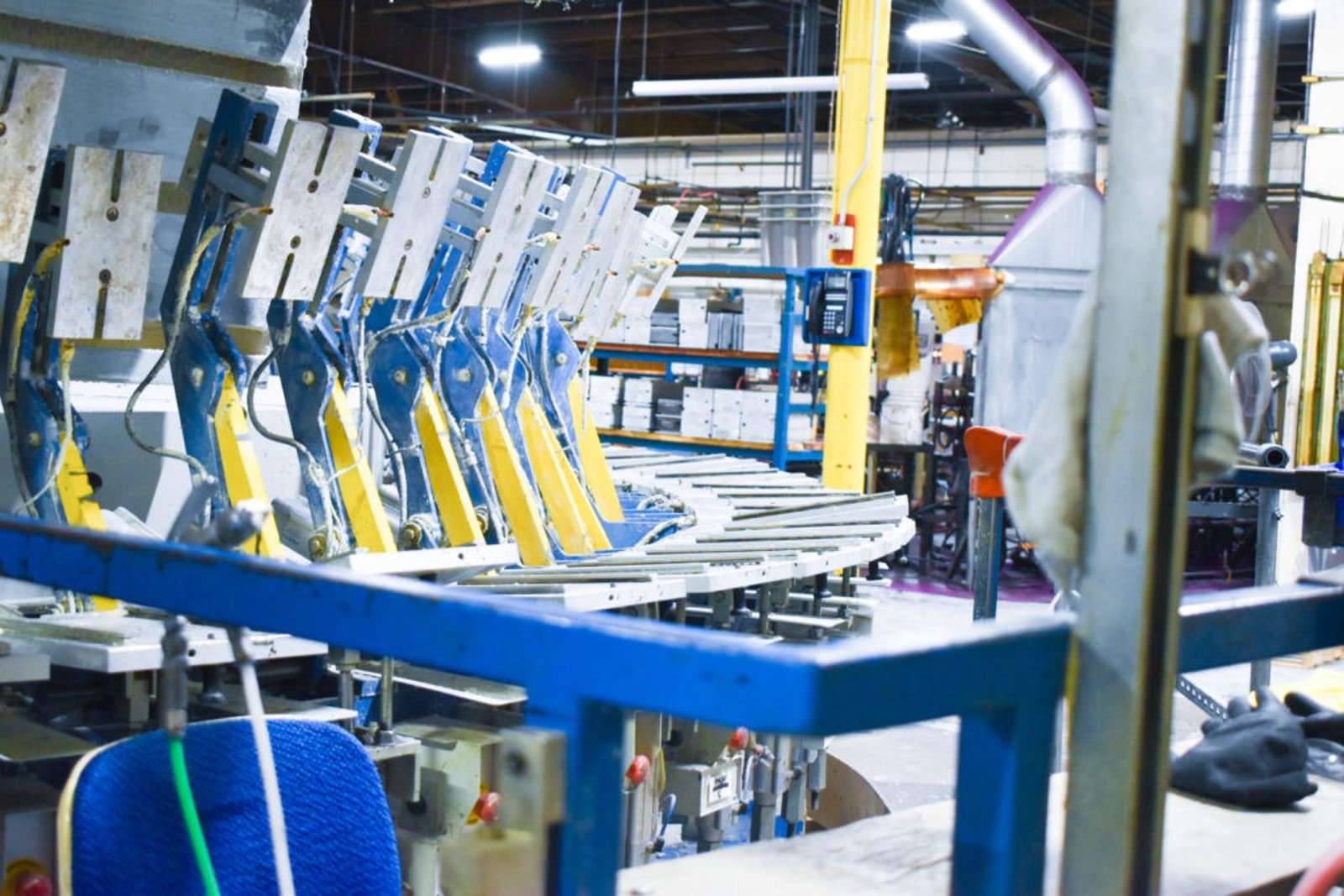
Please do not leave this page until complete. This can take a few moments.
The new owner of a polymer manufacturing company in Lewiston has doubled its workforce in 100 days and anticipates the surge in personnel and overall production to continue through 2022.
Polymer Laboratories and Solutions LLC, or Poly Labs, was established last November when a group of Maine investors, led by Windham-based Anania & Associates, acquired the 88,000-square-foot manufacturing facility, equipment and intellectual property of plastic maker Jones & Vining, for $5.5 million.
Coinciding with the workforce announcement was the appointment of Sarah Morrison as CEO.
Morrison brings 15 years of operations and management experience to Poly Labs, where she previously held the role of chief operations officer, according to a news release.
By the time the deal closed, on Nov. 2, Jones & Vining had begun laying off personnel and was planning to close the facility, citing the impact of the pandemic, Scott Knoll, a partner with Anania & Associates, told Mainebiz at the time. Before the pandemic, the plant employed about 80 people. After layoffs, the workforce was in the 30-plus range.
Jones & Vining, which retains its Massachusetts headquarters and its plants in Asia, had a longstanding mix of industrial and medical customers and products, including high-quality noise-canceling foam made for Bose military headsets. Hundreds of thousands of parts came out of the plant in a typical year. The ownership team decided the investment was worthwhile.
But the first month was a bit slow, Knoll said.
“It turns out that customers were a bit nervous,” he said. “Then December hit and everything just exploded. Part of it was getting set up in their systems and then proving to them that we would be back up and running.”
The new owners worked to restore business to previous levels but also beyond that, reaching out to existing and prospective customers, launching a new website, writing job descriptions for new hires and planning construction updates on the facility.
By December, once the plant was back up and running and key personnel were in place, existing customers returned and new customers started coming in, he said.
The workforce started out in the mid- to high 20s and is now fast climbing past 50.
“We’re hiring as fast as we can, to keep up,” said Knoll.
Hiring so far has included machine operators, process leads, lab technicians, engineers, maintenance personnel and others.
Currently, there are six production positions open.
“Production is just about doubling every month,” said Knoll. “We’re getting back up an beyond the previous levels. In January, a couple hundred thousands parts got shipped out. This month, we’ll double that.”
Poly Labs is one of the last U.S. producers of very small precision polyurethane parts.
The company designs and manufactures highly engineered molded, self-skinning and small pour polyurethane, thermoplastic polyurethane, thermoplastic elastomer and thermoplastic rubber components. Products reach customers in various markets, including defense, medical, footwear and impact protection applications.
Examples include interior impact pads for sports and military helmets, outsoles for shoes and medical pillows.
The company reaches new customers through outlets such as its new website, LinkedIn, press releases and industry affiliations.
“We’re getting two or three new leads per day, all domestic,” said Knoll.
Through an expanded workforce, the company plans to increase production capacity, offer a wider base of polyurethane products and enhance plant capabilities.
Workforce recruitment has included hiring back employees who had moved on from their previous Jones & Vining positions as a result of the organization’s downsizing.
“They were available for work and interested in coming back,” said Morrison. “We were lucky to have a pool of people who were trained and interested in coming back.”
Other channels include staffing agencies, LinkedIn, networking opportunities and posting jobs on the job search website Indeed.
In the next two months, the company plans to add 10 to 15 employees, said Morrison. By the end of 2021, the workforce could number in the 70s, she added.
To keep up with growing demand, the company is developing options such as swing shifts and second shifts to the standard Monday through Thursday workweek, said Knoll.
The $5.5 million investment included working capital as well as the acquisition of the business.
That includes upgrades to the facility, including investment into its existing research and development lab, a major refresh of the employee break room and bathrooms and, expected in June, installation of a large new polyurethane system of machinery for added capacity.
The company offers both robotic production and lab equipment, along with older legacy processing lines and machines. That includes a 60-station twin-head polyurethane molding machine used for manufacturing and molding footwear outsoles, insoles and midsoles; over a dozen other large polyurethane production machines, some fully robotic and other manually operated; 20 injection molding machines; and a large lab for material characterization, material research, product development and quality control.
The company is looking into automation and other equipment improvements, said Morrison.
“We’re operating with a lot of older equipment that might not be as efficient as it could be,” she said.
For example, the current equipment requires operator interaction to some extent.
“That could be spraying mold reliefs, or removing parts from the mold, or trimming parts as they come off a mold,” she explained. “All those actions are repetitive and can take time.”
This is great news! Jones and Vinning have been apart of the Lewiston/Auburn manufacturing community for many years. It is good to see more innovation and support fir the company.
The Giving Guide helps nonprofits have the opportunity to showcase and differentiate their organizations so that businesses better understand how they can contribute to a nonprofit’s mission and work.
Learn MoreWork for ME is a workforce development tool to help Maine’s employers target Maine’s emerging workforce. Work for ME highlights each industry, its impact on Maine’s economy, the jobs available to entry-level workers, the training and education needed to get a career started.
Learn MoreWhether you’re a developer, financer, architect, or industry enthusiast, Groundbreaking Maine is crafted to be your go-to source for valuable insights in Maine’s real estate and construction community.
Learn moreThe Giving Guide helps nonprofits have the opportunity to showcase and differentiate their organizations so that businesses better understand how they can contribute to a nonprofit’s mission and work.
Work for ME is a workforce development tool to help Maine’s employers target Maine’s emerging workforce. Work for ME highlights each industry, its impact on Maine’s economy, the jobs available to entry-level workers, the training and education needed to get a career started.
Whether you’re a developer, financer, architect, or industry enthusiast, Groundbreaking Maine is crafted to be your go-to source for valuable insights in Maine’s real estate and construction community.
In order to use this feature, we need some information from you. You can also login or register for a free account.
By clicking submit you are agreeing to our cookie usage and Privacy Policy
Already have an account? Login
Already have an account? Login
Want to create an account? Register
In order to use this feature, we need some information from you. You can also login or register for a free account.
By clicking submit you are agreeing to our cookie usage and Privacy Policy
Already have an account? Login
Already have an account? Login
Want to create an account? Register
This website uses cookies to ensure you get the best experience on our website. Our privacy policy
To ensure the best experience on our website, articles cannot be read without allowing cookies. Please allow cookies to continue reading. Our privacy policy
1 Comments