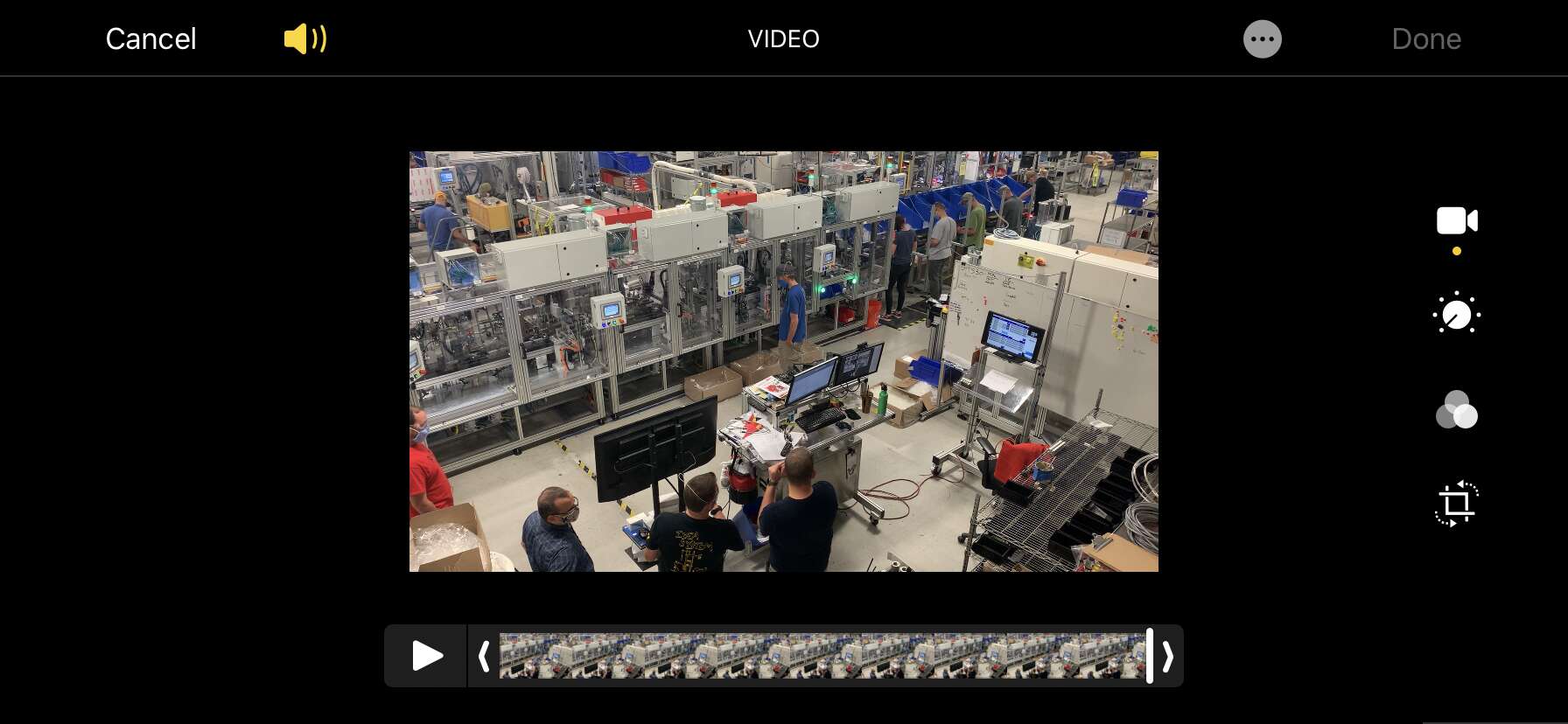
Please do not leave this page until complete. This can take a few moments.
Typically, when Lanco Integrated completes construction of a new machine, the Westbrook manufacturer invites the customer to an onsite “factory acceptance test” that determines if the device fulfills specified performance requirements.
During the pandemic, Lanco has limited visits to its factory. So the company, which makes robotic mass-assembly systems, developed a virtual testing protocol with a system of cameras on its assembly lines that allow for live video sessions with customers.
“We had to adapt and make that happen for them as best as possible virtually,” Matt Mingo, a manufacturing project leader, told Mainebiz.
The manufacturing department made the switch by working with the information technology department, which produced multiple video feeds for a live streaming Zoom call, Mingo explained.
One factory test ran for four hours and required multiple points of view around the machine. Mingo and others on the manufacturing team used their mobile devices to zoom into machine details.
“If they had a question, we could walk to a specific point on their machine and give them details,” he said.
There was also a live audio feed and live chat function, so manufacturer and customer could correspond throughout the test. The goal is to provide optimal transparency, said Stew Goss, the firm’s global information technology manager.
The virtual system used a combination of tools that included mini wireless security cameras and USB laptop cameras, as well as several dedicated computers to join the Zoom call and share the video, explained Goss. The customer could see each part of the machine’s functioning as it was happening.
Goss and his department performed a second virtual test using Microsoft Teams as the platform.
“We’re trying to refine the process,” he said. “Right now I go in there to put all of the pieces of the puzzle together.”
The company is thinking about making the virtual test system a permanent part of its services.
“It’s a time-saver,” Goss said. “Lots of companies are international. It’s not cheap to send their teams over here.”
Currently, someone on the factory floor has to manually change camera views and zoom in on details.
“I’d like to put the customer in the driver’s seat,” Goss said of the system’s potential for allowing customers to “drive” the cameras.
Lanco declined to say who the customers were.
In June, Lanco got an initial taste of pushing the boundaries during the pandemic when it manufactured a machine that puts together critical coronavirus test components in just eight weeks — a job that would typically have taken 35 weeks.
The Giving Guide helps nonprofits have the opportunity to showcase and differentiate their organizations so that businesses better understand how they can contribute to a nonprofit’s mission and work.
Learn MoreWork for ME is a workforce development tool to help Maine’s employers target Maine’s emerging workforce. Work for ME highlights each industry, its impact on Maine’s economy, the jobs available to entry-level workers, the training and education needed to get a career started.
Learn MoreWhether you’re a developer, financer, architect, or industry enthusiast, Groundbreaking Maine is crafted to be your go-to source for valuable insights in Maine’s real estate and construction community.
Learn moreThe Giving Guide helps nonprofits have the opportunity to showcase and differentiate their organizations so that businesses better understand how they can contribute to a nonprofit’s mission and work.
Work for ME is a workforce development tool to help Maine’s employers target Maine’s emerging workforce. Work for ME highlights each industry, its impact on Maine’s economy, the jobs available to entry-level workers, the training and education needed to get a career started.
Whether you’re a developer, financer, architect, or industry enthusiast, Groundbreaking Maine is crafted to be your go-to source for valuable insights in Maine’s real estate and construction community.
In order to use this feature, we need some information from you. You can also login or register for a free account.
By clicking submit you are agreeing to our cookie usage and Privacy Policy
Already have an account? Login
Already have an account? Login
Want to create an account? Register
In order to use this feature, we need some information from you. You can also login or register for a free account.
By clicking submit you are agreeing to our cookie usage and Privacy Policy
Already have an account? Login
Already have an account? Login
Want to create an account? Register
This website uses cookies to ensure you get the best experience on our website. Our privacy policy
To ensure the best experience on our website, articles cannot be read without allowing cookies. Please allow cookies to continue reading. Our privacy policy
0 Comments