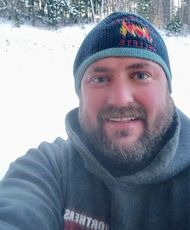
Please do not leave this page until complete. This can take a few moments.
Northeast Pellets in Ashland has emerged from a devastating fire in 2017 with new and larger buildings and a recently installed automation that has allowed the pellet manufacturer to add shifts and expand production.
The Aroostook County company makes heating pellets for residential, commercial and institutional use from organic bark-free mill residuals — sawdust, shavings and chips — produced during the lumber manufacturing process. By using the byproduct, the company said it doesn’t put added pressure on standing forests.
The company also recently announced that it is the first pellet manufacturer in Maine to receive Forest Stewardship Council chain-of-custody certification and one of the first heating pellet firms nationally to achieve the certification.
Over the past few years, the company has noticed increased retailer and consumer demand for council-certified fiber in both the paper and lumber industry, said President and CEO Matt Bell, a 2009 Mainebiz NEXT List honoree.
Mainebiz asked Bell about how he rebuilt the business and what the certification means for the company. Here’s an edited transcript.
Mainebiz: How do you expect Forest Stewardship Council certification to benefit your business?
Matthew Bell: We purchase mill residuals from local sawmills in our area. We’ve known for some time that large landowners and mills have been certified. For them, it was a requirement from big-box stores like Home Depot and Lowe’s, to reassure customers that best forest practices were being used.
I was exploring opportunities for export. That didn’t end up working out. But I found out that, in order to export, you have to have a couple of different certifications. That’s what got me engaged in looking at the Forest Stewardship Council.
Mainebiz: What’s involved in getting chain-of-custody certification?
Bell: I have to show we’re purchasing mill residuals from certified mills, and I track it. If I bring in non-certified wood, we can’t sell it with the FSC logo on the bag.
We currently sell to Home Depot, Tractor Supply, Lowe's and Sam’s Club. We also sell bulk to local colleges and universities such as Northern Maine Community College in Presque Isle and the University of Maine at Fort Kent. Walmart recently committed to sourcing FSC products.
Mainebiz: How will you use the certification to build business?
Bell: We’ll promote the fact that we’re certified. That should help us gain market share.
Mainebiz: Are you seeing strong consumer demand for certified wood products?
Bell: We are the only mill in Maine and, as near as I can tell, we’re one of three heating pellet mills in the U.S that have the certification. So we’ll be ahead of the curve when and if the big-box stores start requiring it. But I’ve gotten a lot of great feedback from consumers and people in industry who are familiar with the program, because they know the certification is significant for forest management.
Mainebiz: The company opened in 2006 and has suffered two fires since then, in 2009 and 2017. Could you describe the rebuilds?
Bell: My father and I first broke ground for the company in 2004 and had the original facility all under one roof. In the first fire we lost our office and shop. When we rebuilt, we separated our operations to mitigate our risk. So we had seven buildings when we came back online. Rebuilding is hard, but it’s even harder when you lose your office with all your documents.
The 2017 fire destroyed our processing and packaging facilities. But it was at least contained to those two buildings. That made the overall value of the loss that much less, and made the process of rebuilding that much faster and easier.
Mainebiz: How did you finance the rebuild?
Bell: We exhausted our insurance proceeds, did the design ourselves and, with a small crew and a couple of contractors, did the construction and equipment installation ourselves.
Before the fire, we had 13 or 14 employees and were producing around 15,000 tons of pellets annually. A couple of employees stayed during the cleanup and rebuilding process and we laid off the other employees.
Mainebiz: When did you get back into business?
Bell: In December 2018. So 2019 for us was kind of starting up and getting our feet back under us, getting the bugs worked out of the system, gaining back our customer base and our fiber supply. Being offline for over a year, customers who needed the product had to go somewhere else. Same with the mills we buy the residuals from: They needed to move the product so they had to go somewhere else.
Mainebiz: Was there a silver lining to the rebuild, as far as upgrading infrastructure?
Bell: We put in steel buildings instead of wood-frame. We made our processing facility a little bit larger, with a little bit higher output capacity. And for our packaging building, went from 2,500 square feet to 12,000 square feet.
Mainebiz: Why so much bigger?
Bell: For storage of finished product and packaging supplies to keep them out of the elements. Previously, a lot of it was stored outside. Or we’d order a lot of the supplies on a just-in-time basis. Now we’re able to order larger quantities and realize savings in bulk purchasing.
Mainebiz: So you were on the way to full recovery in 2019. Then the pandemic hit. What happened?
Bell: We were on track to increase production for the heating season of 2019 into 2020. Then COVID hit. Unfortunately, it affected our business. When the universities shut down, they still took some pellets to heat their campuses. But demand was much lower.
We also had staffing issues. Forest products was considered an essential industry and we had a few people who got done because they didn’t want to be exposed. We also had to shut down a couple of times for quarantining because of a potential exposure.
Last summer, we had multiple openings listed that paid well, but we struggled to fill them. But I had looked at an automated packaging line with a robot stacker and an automatic wrapper. Previously, we weren’t quite large enough and didn’t have enough volume to justify the purchase. But when we were forced to shut down last summer, there was a full month when we did production one day and packaging the next day, alternating back and forth day by day because we didn’t have enough staffing to run both lines full-time simultaneously.
So we made a large investment to put in an automated packaging line, which allowed us last fall to go to production 24 hours, four days a week.
I’ve always been a strong advocate for hiring people and doing on-the-job training. But over the years, the labor pool hasn’t been there, so this is something that’s been a while coming. The pandemic pushed us to that point.
Mainebiz: Did the space you built after the 2017 fire accommodate the line?
Bell: Yes. Even though we didn’t put in a fully automated packaging line from the start, I designed and laid things out, and the building was large enough, so that we could put in the new line last fall without having to do renovations or additions.
Mainebiz: What’s production looking like now?
Bell: We have 12 employees and we’re on track to produce close to 25,000 tons. The automated equipment, rather than replacing people, has allowed us to increase production and keep up with packaging, and we’ve shifted those people to a second shift for production.
The automated line requires two people to operate efficiently. Before, when we were packaging manually, we were running with three to four people and they were doing 5-7 tons per hour. Now we’re doing around 10-12 tons per hour with two people. It’s essentially doubled throughput with half the labor.
Mainebiz: How big is the pellet industry in Maine?
Bell: Four pellet mills in Maine have a combined production of 220,000 to 250,000 tons.
Mainebiz: How big is the market?
Bell: We ship throughout the Northeast and as far as Pennsylvania, New York, Rhode Island, a lot into Massachusetts and New Hampshire, as well as Maine.
But this past year, with low fuel prices and a very mild winter, what started off as a very good season last fall and into the early winter dropped off after the first of the year. Back in November, if fuel prices had climbed up like they are today, we would have had more demand. As fuel prices climb, pellets are stable pricewise. We predict that, next season with higher fuel prices, demand for pellets will be that much greater. A lot of people have pellet stoves for supplemental heating. In a cold year when fuel prices are high, they’ll burn 4-5 tons of pellets. In a mild year when fuel prices are low, that same person might only burn one ton.
0 Comments