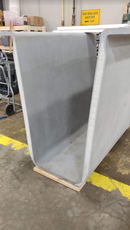
Please do not leave this page until complete. This can take a few moments.
AIT Bridges, based in Brewer, on Tuesday unveiled a new bridge girder made of composite materials, and says the product is lighter and longer-lasting than traditional concrete and steel girders.
The new component is called a tub girder, and is an extension of the composite bridge systems offered by AIT Bridges, a division of Advanced Infrastructure Technologies.
The system, developed in cooperation with the University of Maine’s Advanced Structures and Composites Center, was created to provide an affordable, long-term solution for traditional steel and concrete medium-span deck bridges. Ultimately, AIT hopes the products will replace concrete and steel girders in the marketplace.
AIT is now manufacturing girders for its first such span, to be constructed in Hampden.
The tub girder is made with a lightweight fiber-reinforced polymer. The girders are supported on standard foundations for bridges that include either a precast concrete panel deck or a cast-in-place concrete bridge deck.
According to the release, the girder can be used for a variety of spans up to 100 feet, and offers several advantages.
• Sustainability: The manufacturing process and installation have a smaller carbon footprint than those of conventional steel and concrete girders.
• Longevity: The girder is expected to last 100 years or more. It is naturally corrosion-resistant and made of materials designed to overcome many environmental hazards. The girder requires little or no maintenance.
• Weight: The girder is 50% lighter than steel and 75% lighter than concrete girders. The weight reduction allows for a decrease in large equipment on the construction site and significantly reduces transportation costs.
• Affordability: The girder is expected to have the lowest maintenance cost in the industry, and a much lower initial cost compared to similar steel and concrete solutions.
AIT Bridges is a division of Advanced Infrastructure Technologies, a designer and supplier of composite bridge systems and structural components for commercial construction. AIT Bridges systems utilize components from technology developed over an 11-year period by the Advanced Structures and Composites Center at the University of Maine. The goal was to develop a rapidly deployable bridge technology for the military. In 2008, Advanced Infrastructure Technologies was formed to commercialize an inflatable arch technology. AIT Bridges expanded the composite product line and designed a composite arch bridge system built from the original technology.
The Giving Guide helps nonprofits have the opportunity to showcase and differentiate their organizations so that businesses better understand how they can contribute to a nonprofit’s mission and work.
Learn MoreWork for ME is a workforce development tool to help Maine’s employers target Maine’s emerging workforce. Work for ME highlights each industry, its impact on Maine’s economy, the jobs available to entry-level workers, the training and education needed to get a career started.
Learn MoreWhether you’re a developer, financer, architect, or industry enthusiast, Groundbreaking Maine is crafted to be your go-to source for valuable insights in Maine’s real estate and construction community.
Coming June 2025
Learn moreThe Giving Guide helps nonprofits have the opportunity to showcase and differentiate their organizations so that businesses better understand how they can contribute to a nonprofit’s mission and work.
Work for ME is a workforce development tool to help Maine’s employers target Maine’s emerging workforce. Work for ME highlights each industry, its impact on Maine’s economy, the jobs available to entry-level workers, the training and education needed to get a career started.
Whether you’re a developer, financer, architect, or industry enthusiast, Groundbreaking Maine is crafted to be your go-to source for valuable insights in Maine’s real estate and construction community.
Coming June 2025
In order to use this feature, we need some information from you. You can also login or register for a free account.
By clicking submit you are agreeing to our cookie usage and Privacy Policy
Already have an account? Login
Already have an account? Login
Want to create an account? Register
In order to use this feature, we need some information from you. You can also login or register for a free account.
By clicking submit you are agreeing to our cookie usage and Privacy Policy
Already have an account? Login
Already have an account? Login
Want to create an account? Register
This website uses cookies to ensure you get the best experience on our website. Our privacy policy
To ensure the best experience on our website, articles cannot be read without allowing cookies. Please allow cookies to continue reading. Our privacy policy
0 Comments