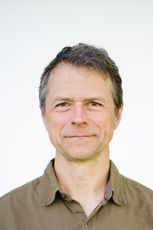
Please do not leave this page until complete. This can take a few moments.
GO Logic LLC, a Belfast-based business specializing in passive house architecture and construction, is proposing to build a new production facility and headquarters that will be at least three times larger than its combined space at three different sites.
“We don’t have the capacity for all the projects we’d like to build now,” Alan Gibson, a founder and principal with the firm, told Mainebiz. “That’s the impetus for this move.”
The new “panelization” facility will be used to pre-fabricate wall panels and other components.
The company’s current panelization shop occupies a 3,500-square-foot lease in Waldo. It recently opened a small shop and warehouse space at 40 Center St. in Scarborough. And its office headquarters is a 1,200-square-foot lease at 137 High St. in downtown Belfast.
Now it’s in the design and permitting process for a 19,000-square-foot facility on two lots at 52 Little River Drive in the Belfast Airport Business Park. The company purchased the lots a year ago.
The proposal comprises 16,000 square feet of factory floor and an attached 3,000 square feet or so of office space.
The company would give up its Waldo and downtown Belfast leases, Gibson said.
Overall investment in the new facility is expected to be around $2 million. Financing would be through loans with the U.S. Small Business Administration and a private bank, he said.
The goal is to break ground in the next month or so and to be in the new facility by late spring 2022.
Instead of delivering stacks of building materials to a construction site and assembling them out in the elements, panelization involves constructing exterior wall panels up to 30 feet long, as well as interior walls and wood floors, indoors under climate-controlled conditions, according to the company’s website.
The panels, complete with building wrap, windows, and exterior insulation installed, are then delivered to the building site and craned into place on a foundation that has been constructed in advance. A prefabricated-truss roof follows, yielding a weathertight, air-sealed building shell in less than two weeks of on-site construction
The panels are built to passive house standards for a high level of thermal performance while passively managing moisture originating outside and inside the building. Construction includes a thick layers of insulation, sheathing and sealing.
On houses built for Maine clients, panelization permits greater control over schedule and delivery. For projects outside of Maine, it allows the company to offer its design and passive house construction in an off-the-shelf package for local builders.
“We’ve been panelizing buildings for about the last four years in Waldo, which we’ve outgrown,” said Gibson. “That’s the reason for the new space in Belfast.”
GO Logic designed the new facility and will serve as general contractor. Unsurprisingly, the building will be super-insulated and air-tight with a very low energy load.
GO Logic recently received a $240,000 grant toward the purchase of equipment at the planned facility. The money was awarded by the federal Community Development Block Grant, a U.S. Housing and Urban Development economic development program. The program requires the business to supply matching funds in at least a 2:1 ratio. GO Logic has said it has secured the $120,000 in the form of cash on hand.
As required by the application process, the city of Belfast applied for the grant on GO Logic’s behalf. The city council accepted the funds at its meeting earlier this month.
The company plans to use the money to pay for part or all of two “butterfly tables” — specialized tables used in manufacturing processes to aid in the construction of wall and roof panels — and a specialized forklift designed to efficiently and safely transport the fabricated panels around the production area.
Butterfly tables are used in manufacturing processes to more easily position and manipulate fabricated panels that may be otherwise unwieldy due to their size and/or weight.
The grant program also requires the business to create one full-time equivalent position per $30,000 of grant funding received, with at least 51% of those new positions being taken by individuals from low- to moderate-income households, which are households making less than 80% of the county median income.
For GO Logic, that means creating eight full-time jobs, at least five of which will be taken by individuals from low- to moderate-income households.
“We won’t have any problem meeting that requirement,” said Gibson.
The company recently added several employees who will count toward the required eight. It’s now up to about 40 employees.
Additional positions are available, mostly in panel production, as well as two designers and a project manager and/or salesperson, he said.
Recruitment plans include a mix of ads, social media and web-based recruiters such as Indeed.
“Often people just find us,” he said. “We’ve had some luck with people moving to Maine to work for us. They’re interested in the company and what we do. And/or they moved to Maine recently, found us and like what we do. We’re able to take advantage of our position in the market and our particular niche.”
The company’s “bread and butter” projects are its pre-designed lines of “GO Homes.”
“That’s the vast majority of what we do,” Gibson said. “We do allow a certain amount customization.”
Most projects take place along the coast from Belfast to Portland, with the occasional jobs on Mount Desert Island and elsewhere. Within an approximately 50-miles radius of Belfast, GO Logic serves as the general contractor.
The company also creates and delivers complete shell packages to clients outside of that range in Maine and in other states, including New York, Connecticut, Massachusetts, Rhode Island, New Hampshire and Vermont. In those instances, the company partners with local general contractors to install the package.
The company averages 20 to 25 projects in the design-and-build pipeline per year, with another six to 10 complete homes or shell packages shipped per year.
It’s expected those numbers will at least double in the new facility, said Gibson.
Looking to the future, and as new construction continues to be increasingly expensive, the company’s goal is to make its projects more affordable to more people, he continued.
“They’re not a low-end product, but we’re trying to bring the performance, comfort and durability to the market at a price point that’s comparable to other custom homes that don’t have the same level of efficiency and quality,” he said. “The way to do that is through efficiencies of panelizaion and more mass production, which we’ll be able to achieve in our new facility.”
Panelization also saves at least four to six weeks of time compared with on-site construction, he said.
“The big advantage of panelization is you’re doing all of the work indoors in a controlled environment,” he said. “You have a much drier, cleaner, more precise product when you’re done. We can put together a shell package for a typical house in seven to 10 days.”
Gibson and his former business partner, architect Matt O'Malia, are Mainebiz 2014 NEXT List honorees.
They founded GO Logic in 2008 as the first company in Maine — and 12th in the United States — to be certified by the Passive House Institute U.S. to design and build “passive homes” that meet the highest international standard for energy efficiency.
0 Comments