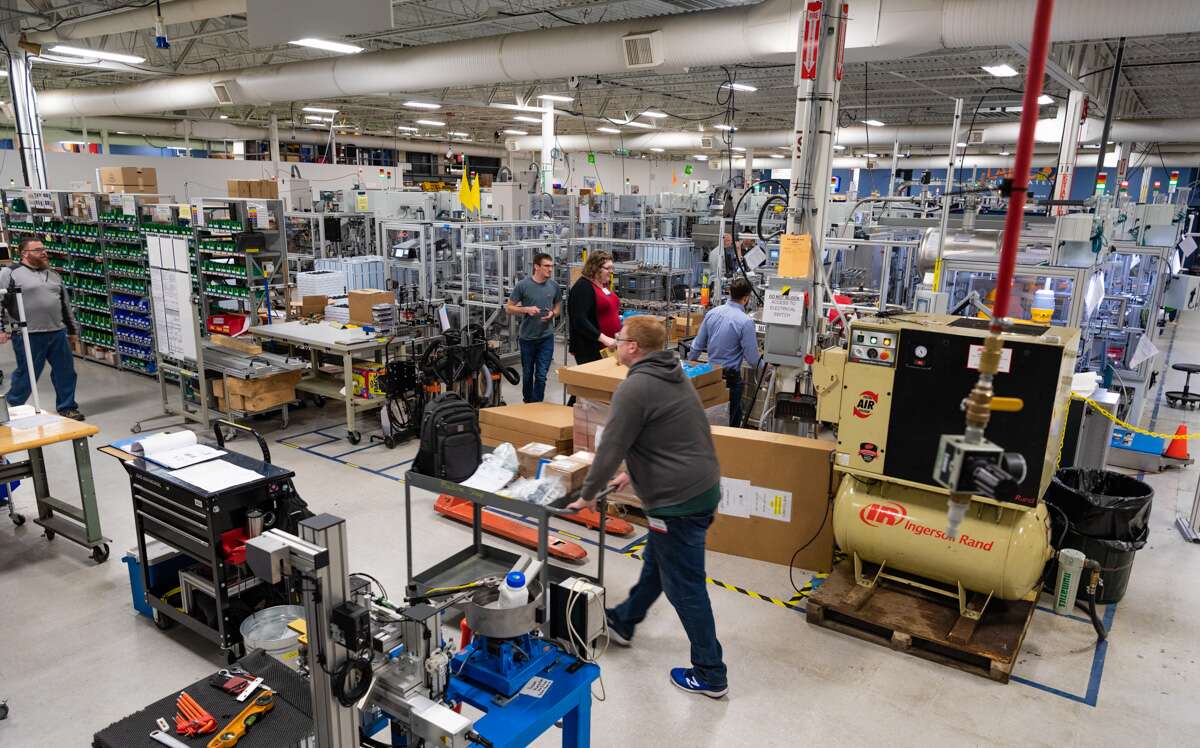
Please do not leave this page until complete. This can take a few moments.
At Lanco Integrated in Westbrook, manufacturing project leader Peter Brazier was a cabinetmaker and house builder in a former life.
When the 2008 financial crisis hit, he went back to school, enrolling in Southern Maine Community College’s industrial technology program while completing two internships at Lanco. Eight years ago, when he graduated, he started full-time at Lanco and has been there ever since.
“I like that you’re constantly challenged,” Brazier says while working on a machine that will be used to make shower valves. “The technology is changing so much, you have to know every machine inside out.”
That’s evident as he points to tiny parts in a vibrator feeder bowl, explaining how they move around when the machine is on. Besides the fast-paced work environment, he relishes travel to Germany and Hong Kong — a perk of working for a global company.
Like Brazier, many Lanco employees are former interns. The company, with a workforce of 183 in Westbrook and 300 total, designs and makes machines and test systems used by manufacturers in sectors including automotive and medical.
With the vast majority of its customers outside of Maine including overseas, the employee-owned firm lacks the name recognition of bigger manufacturers based here, or nearby IDEXX Laboratories.
That’s prompted Lanco to take a more proactive, long-term approach to recruiting and workforce development. Strategies include tapping Maine’s community and public colleges for summer interns and entry-level jobs; hosting factory tours for school groups from elementary through college level and mentoring high school robotics teams; and limited recruiting in New Hampshire. It has also provided machines for students to work on at the University of Maine’s Advanced Manufacturing Center in Orono.
“We’ve struggled in the past getting people to move to Maine,” says Lanco President and CEO Ed Karabec, who’s led the company for 30 years. “Going to Detroit and trying to bring people to Maine is not a solution. The only way we can develop our workforce is with recent graduates.”
The company has hired more than 50 University of Maine System alumni.
“Even if they don’t come back,” Karabec says, “they go back and speak about their experience here about what they’ve been able to do. If you like working with your hands, and you like designing things, that’s what we do every day.”
That leaves the company no choice but to tap a younger talent pool to expand its workforce since there are now very few automation companies in the area.
“If somebody wants to do this work, and they’re older, they’re here already,” says Karabec.
Its efforts appear to be paying off as reflected in a younger workforce, with a median age of 41.85 years — below the 44.9 U.S. median age of manufacturing workers.
Lanco Integrated’s immediate hiring needs are for a controls programmer and global customer services manager.
Karabec, who comes from an engineering background, says that software programmers are the hardest jobs to fill, and require a fair amount of training.
He also says those jobs involve a lot of travel. He sees that as a draw for younger hires, along with the variety of the work.
“We build 40 pieces of capital equipment in a year,” he says. “Our customers use the same piece of capital equipment for 10 or 20 years. For somebody who likes to do this type of work, it’s a constant new refresh.”
All new hires, regardless of department and position, are required to spend three to six months on the factory floor to gain a more well-rounded perspective by starting “at the bottom,” as Karabec puts it.
“It was enlightening for sure,” mechanical engineer Giovanna Patrizio says of her experience, “because we see our designs firsthand and you think, ‘Ah, I will design that a little bit differently now.” A 2015 graduate of the Rochester Institute of Technology, Patrizio moved to Maine for family reasons and landed at Lanco initially through a staffing agency before she was hired.
She spent her first three months on the job at Lanco’s Hong Kong division and now oversees global training that uses a wiki platform she’s in the process of updating.
“There’s a lot of experience here that is with people, and we’re trying to disseminate that knowledge so it’s not just in people’s heads,” says manufacturing manager Mitch Sanborn.
Sanborn says there’s also on-the-job training for engineers through a rotating quarterly position in the factory, to “make sure that engineers talk to the technicians and vice versa.”
Lisa Martin, executive director of the Manufacturers Association of Maine, told Mainebiz she sees the sector’s biggest workforce challenge as “finding people that are willing to work, have the skills and show up every day with aptitude to learn and grow with the company.”
Her advice to employers: “Look towards both the traditional workforce and new populations here in Maine, including returning military members, new Mainers and Fedcap participants that are seeking career opportunities in Maine.” For those that don’t know, Fedcap Rehabilitation Services Inc. is a New York-based nonprofit that provides vocational training and employment resources to those facing barriers to employment.
Geography: Headquartered in Westbrook, with design, manufacturing, assembly and sales facilities in Stuttgart, Germany; Hong Kong; and Shanghai, China.
What it makes: Turnkey automated assembly and test systems for sectors including automotive and medical.
Ownership: Employees
Leadership: Ed Karabec, president and CEO
Workforce count: 300 total including 183 in Westbrook
Contact: www.lanco.net
The Giving Guide helps nonprofits have the opportunity to showcase and differentiate their organizations so that businesses better understand how they can contribute to a nonprofit’s mission and work.
Learn MoreWork for ME is a workforce development tool to help Maine’s employers target Maine’s emerging workforce. Work for ME highlights each industry, its impact on Maine’s economy, the jobs available to entry-level workers, the training and education needed to get a career started.
Learn MoreWhether you’re a developer, financer, architect, or industry enthusiast, Groundbreaking Maine is crafted to be your go-to source for valuable insights in Maine’s real estate and construction community.
Coming June 2025
Learn moreThe Giving Guide helps nonprofits have the opportunity to showcase and differentiate their organizations so that businesses better understand how they can contribute to a nonprofit’s mission and work.
Work for ME is a workforce development tool to help Maine’s employers target Maine’s emerging workforce. Work for ME highlights each industry, its impact on Maine’s economy, the jobs available to entry-level workers, the training and education needed to get a career started.
Whether you’re a developer, financer, architect, or industry enthusiast, Groundbreaking Maine is crafted to be your go-to source for valuable insights in Maine’s real estate and construction community.
Coming June 2025
In order to use this feature, we need some information from you. You can also login or register for a free account.
By clicking submit you are agreeing to our cookie usage and Privacy Policy
Already have an account? Login
Already have an account? Login
Want to create an account? Register
In order to use this feature, we need some information from you. You can also login or register for a free account.
By clicking submit you are agreeing to our cookie usage and Privacy Policy
Already have an account? Login
Already have an account? Login
Want to create an account? Register
This website uses cookies to ensure you get the best experience on our website. Our privacy policy
To ensure the best experience on our website, articles cannot be read without allowing cookies. Please allow cookies to continue reading. Our privacy policy
0 Comments