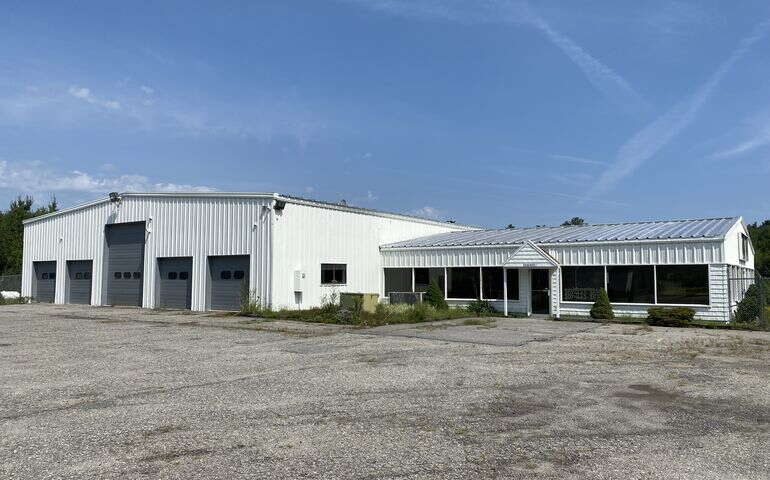
Please do not leave this page until complete. This can take a few moments.
The manufacturer of a composite board and building system called Edura is expanding from a 1,200-square-foot space in Nobleboro to a 14,750-square-foot lease in Woolwich.
Even Keel Inc. leased the industrial space at 126 U.S. Route 1 from Woo Industrial LLC.
Tim Millett of Porta & Co. brokered the transaction.
The building, on 5.4 acres, includes eight drive-in doors and has great visibility on U.S. Route 1, according to the listing.
The location was previously leased by Carvana, the online used-vehicle dealer, said Millett.
Before Carvana, previous tenants at different times included BFC Marine and Brothers Chevrolet.
Even Keel, owned by Ben Davis, is the parent company of three complementary and vertically integrated sub-entities that provide construction materials and building systems.
Siblings Ben and Emily Davis founded OpBox in 2018 and were Mainebiz Next List honorees that year.
OpBox initially used shipping containers to adapt to a variety of uses, from retail pop-ups to food vendors to ticket booths.
But in 2020, OpBox production was sharply constricted because the supply of shipping containers from China was cut off and the price from other sources tripled. The Davises looked at traditional stick frame construction for the modular units but found it wouldn’t work for the business.
During a trip to Canada, Davis came upon a building panel that used 100% recycled PET plastic from JD Composites of Nova Scotia, and began using the panel to make OpBox units.
“We used that experience to develop our own panel and spent the last couple of years developing our own recipe to be able to manufacture it closer to home rather than shipping from Canada,” said Davis.
Acadian Composite was born as an OpBox sister company to produce the panels made from recycled plastic sourced from the ocean and landfills.
Edura is marketed as a construction product that accelerates the building cycle, reduces labor needs and reduces environmental impact. Davis said its prefabricated SIP panels provide for quicker assembly and have longer lifespan than traditional wood materials because they’re inert to water, insect and mold damage. The product’s insulation value is superior to traditional materials, he said.
OpBox has been using Edura to build its units through the product’s development iterations over the past few years.
In 2022, the Davises applied a $25,000 award from the pitch competition “Greenlight Maine” to create content for its first OpBox Village in South Boston, a collaboration with two partners and branded as the C Street Pop-Up Iron Works. The village consisted of 80,000 square feet in modular rental spaces intended for retail, food and drink operators.
Last winter, OpBox partnered with L.L.Bean — a frequent customer — on a ticket shack on the west side of Mt. Abram ski area.
With patents for the panels and building system in hand, Davis and his team are now preparing to manufacture Edura at scale in Woolwich.
“The Woolwich facility allows us to open up a new line of business” that includes not only making Edura for OpBox but also for other manufacturers and contractors, he said.
The panels will come in a variety of dimensions and thicknesses.
“Being able to sell these panels and the adhesives and tapes we’ve developed, you have a complete system for the building envelope and also for component such as countertops, cabinets and modular containment walls,” he said.
Fitting up the Woolwich location includes an investment in a lamination line for the composite panels. The line will produce 30,000 square feet of Edura per month with one shift operating. Edura is seeing orders from as far as Austin, Texas. Most orders are going locally and regionally for residential and commercial construction and to use to build components in other systems.
Davis declined to cite the investment in the Woolwich location but said the company is halfway to completing a $2 million Series A capital raise, which is going primarily to equipment and marketing.
“We’re in the middle of the implementation and installation of the manufacturing line,” said Davis. It’s expected the line will be up and running in October. The plant is partially active with OpBox production. The Nobelboro location — which is in a small commercial space on the Davis family’s farm — also continues to make OpBox units.
The Woolwich plant employs about 10 people. It’s expected there will be about 15 by the end of this year and the addition of a second shift by late 2024.
Finding the right spot for the expansion was a bit of a journey.
“We looked for several years for the right spot,” said Davis.
When the Woolwich location hit the market, “We jumped on it,” he said. “It’s the perfect space for what we’re doing. Proximity to our existing team is great. The exposure on Route 1 is awesome for a new business and a new brand. The building layout is perfect. It’s a big rectangle and we can bring in raw materials on one end and bring out the finished product on the other. And there’s plenty of room to expand.”
The Giving Guide helps nonprofits have the opportunity to showcase and differentiate their organizations so that businesses better understand how they can contribute to a nonprofit’s mission and work.
Learn MoreWork for ME is a workforce development tool to help Maine’s employers target Maine’s emerging workforce. Work for ME highlights each industry, its impact on Maine’s economy, the jobs available to entry-level workers, the training and education needed to get a career started.
Learn MoreWhether you’re a developer, financer, architect, or industry enthusiast, Groundbreaking Maine is crafted to be your go-to source for valuable insights in Maine’s real estate and construction community.
Coming June 2025
Learn moreThe Giving Guide helps nonprofits have the opportunity to showcase and differentiate their organizations so that businesses better understand how they can contribute to a nonprofit’s mission and work.
Work for ME is a workforce development tool to help Maine’s employers target Maine’s emerging workforce. Work for ME highlights each industry, its impact on Maine’s economy, the jobs available to entry-level workers, the training and education needed to get a career started.
Whether you’re a developer, financer, architect, or industry enthusiast, Groundbreaking Maine is crafted to be your go-to source for valuable insights in Maine’s real estate and construction community.
Coming June 2025
In order to use this feature, we need some information from you. You can also login or register for a free account.
By clicking submit you are agreeing to our cookie usage and Privacy Policy
Already have an account? Login
Already have an account? Login
Want to create an account? Register
In order to use this feature, we need some information from you. You can also login or register for a free account.
By clicking submit you are agreeing to our cookie usage and Privacy Policy
Already have an account? Login
Already have an account? Login
Want to create an account? Register
This website uses cookies to ensure you get the best experience on our website. Our privacy policy
To ensure the best experience on our website, articles cannot be read without allowing cookies. Please allow cookies to continue reading. Our privacy policy
0 Comments