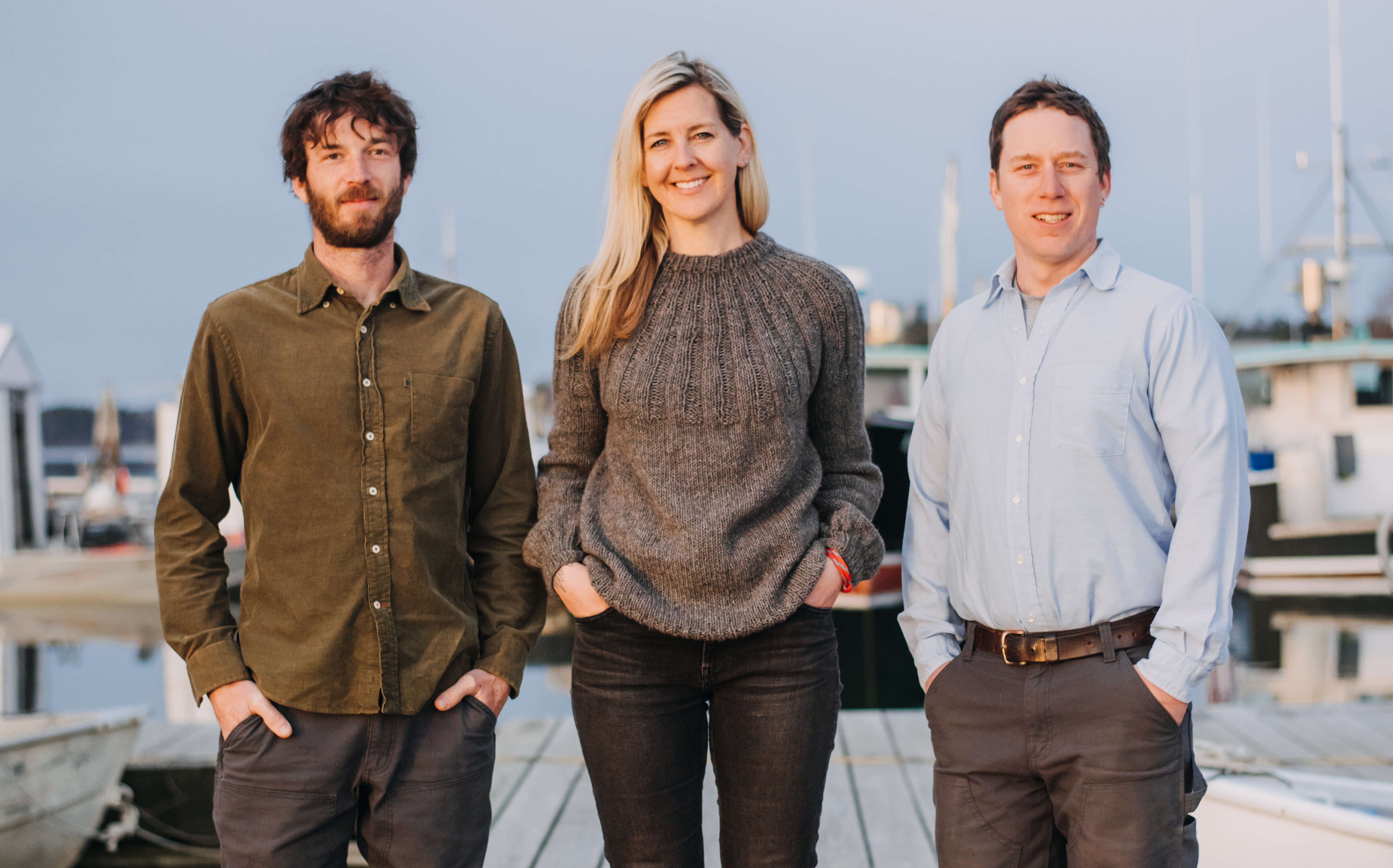
Please do not leave this page until complete. This can take a few moments.
Maine Ocean Farms in Freeport has a mission to embrace new technologies and materials that can drive positive environmental change and support local economic growth.
That includes acquiring a custom-built electric workboat and development of biodegradable and compostable food packaging.
In 2020, in conjunction with a manufacturer in Austria, Maine Ocean Farms created the Ocean Harvest Bag, made from beechwood cellulose fiber, and formed Ocean Farm Supply LLC in Brunswick to distribute the product in the U.S. and Canada.
The fiber is spun into yarn, which is woven into bags designed specifically for the harvest and distribution of shellfish. The bag can be tossed into compost, where it will break down in as little as 12 weeks.
Mainebiz asked Erin Adams, the company’s co-founder and operational CEO, about the product’s roll-out. Here’s an edited transcript.
Mainebiz: How did the idea for biodegradable packaging come about?
Erin Adams: Ocean Farm Supply involves the same players as Maine Ocean Farms — Eric Oransky and Willy Leathers, who started the farm in 2017. The three of us are mariners who worked on tall ships and did oceanographic research. Some of that research was in plastic.
When Eric and Willy stopped shipping out, they still wanted to work on the water, closer to home, so they started the farm. When they started harvesting oysters, they used conventional plastic harvest plastic bags, similar to the mesh onion bags you get at the grocery store. Plastic bags are standard but generate a lot of waste. We wanted an alternative.
MB: How did the idea roll out?
EA: It started with a search — there must be something else on the market. They didn’t find anything else that met the durability and sustainability they were looking for. Then Eric found a manufacturer — PackNatur in Graz, Austria — that provides a similar product for the produce industry.
We worked with them on something especially for shellfish and they negotiated sole distribution rights for the Ocean Harvest Bag, which is trademarked in the U.S and Canada.
That’s when I became involved. I was moving to Maine and finishing up working full-time on the water and doing some research and work in plastic recycling — very complementary to what they were working on. They asked me to get involved and make the business work. We thought if this is a solution for us, then it can work for other shellfish farmers.
MB: What’s the production process?
EA: The material comes from European beechwood that grows in certified forests in Turkey and surrounding countries. The company that makes the yarn, Lenzing, is a leader in cellulose fiber textiles with factories in Germany and Austria. Our manufacturer utilizes that material.
MB: What was your testing process?
EA: We worked with the product they already had and found we liked the material. We knew the weave needed to be stronger to make sure it could hold up to sharp oyster shells. So we worked with them on the design that would work for us.
MB: Did you take part in business development programs?
EA: Since starting selling our Ocean Harvest Bag in April 2021, we have participated in Dirigo Labs Accelerator, Top Gun and, most recently, Food Tech this past fall, where we were connected with great mentors throughout the state.
We also held a desk at the New England Ocean Cluster as part of its Blue Inclusion program funded by Bristol Seafoods. We worked with an Innovate for Maine intern in the summer of 2023, which was an amazing program and an opportunity for us to be connected and supported with an intern for that summer.
MB: What has financing looked like?
EA: We made an initial bootstrap investment of about $25,000. We have received support through Maine Technology Institute and were a recipient of a Thrive forgivable loan last year, which is a huge game-changer for us and is allowing us to work with UMaine's Advanced Manufacturing Center on machinery that will make our operations more time- and cost-efficient.
We were a finalist for the Emerging Business Award in 2022 with Gorham Savings Bank’s LaunchPad program and also a recipient of Preti Flaherty’s Michael Sheehan Memorial Award of $5,000 through our Top Gun class of 2023.
MB: When did the bag become commercially available?
EA: We started making it available to the public in April 2021. Once we figured out the product, we ordered pallets worth. Our manufacturer drops them off by truck in Rotterdam, then it hops onto an Eimskip container ship that goes to Portland, and then we pick them up.
We have a warehouse space of about 1,000 square feet at TechPlace in Brunswick that’s our base of operations, with dry storage, to fulfill orders. It’s the three of us — Eric, Willy and myself, and we are just starting to work with a fulfillment contractor.
MB: How many oysters do you sell now?
EA: This year we planted 1.6 million seeds, so we have about 2.5 million oysters on the farm now. We harvest about 5,000 to 10,000 oysters per week. The majority of our oysters are sold locally, but our oysters have made it as far as California and New Orleans.
MB: What does distribution look like for the bags?
EA: Everything is distributed through TechPlace. We have over 80 customers in shellfish and produce sectors with, most in the Northeast, but also including California, Alaska, Florida and Canada.
MB: How many bags are getting produced?
EA: We produce over 5,000 bags per month. We use some and the majority is sold to other customers.
MB: Plans on the horizon?
EA: The mission is to try to reduce plastic waste in the aquaculture and produce sectors. So we want to grow. Eventually our dream is to figure out how to bring the manufacturing to Maine, but we want to be deliberate as we grow.
MB: Why is reducing plastic in this sector important?
EA: Plastic uses nonrenewable resources and, for shellfish and produce, is single use and then thrown in a landfill. Our product is home compostable. It can be turned right back into soil and go back into the ecosystem. To us, this makes a lot more sense.
The Giving Guide helps nonprofits have the opportunity to showcase and differentiate their organizations so that businesses better understand how they can contribute to a nonprofit’s mission and work.
Learn MoreWork for ME is a workforce development tool to help Maine’s employers target Maine’s emerging workforce. Work for ME highlights each industry, its impact on Maine’s economy, the jobs available to entry-level workers, the training and education needed to get a career started.
Learn MoreWhether you’re a developer, financer, architect, or industry enthusiast, Groundbreaking Maine is crafted to be your go-to source for valuable insights in Maine’s real estate and construction community.
Coming June 2025
Learn moreThe Giving Guide helps nonprofits have the opportunity to showcase and differentiate their organizations so that businesses better understand how they can contribute to a nonprofit’s mission and work.
Work for ME is a workforce development tool to help Maine’s employers target Maine’s emerging workforce. Work for ME highlights each industry, its impact on Maine’s economy, the jobs available to entry-level workers, the training and education needed to get a career started.
Whether you’re a developer, financer, architect, or industry enthusiast, Groundbreaking Maine is crafted to be your go-to source for valuable insights in Maine’s real estate and construction community.
Coming June 2025
In order to use this feature, we need some information from you. You can also login or register for a free account.
By clicking submit you are agreeing to our cookie usage and Privacy Policy
Already have an account? Login
Already have an account? Login
Want to create an account? Register
In order to use this feature, we need some information from you. You can also login or register for a free account.
By clicking submit you are agreeing to our cookie usage and Privacy Policy
Already have an account? Login
Already have an account? Login
Want to create an account? Register
This website uses cookies to ensure you get the best experience on our website. Our privacy policy
To ensure the best experience on our website, articles cannot be read without allowing cookies. Please allow cookies to continue reading. Our privacy policy
0 Comments