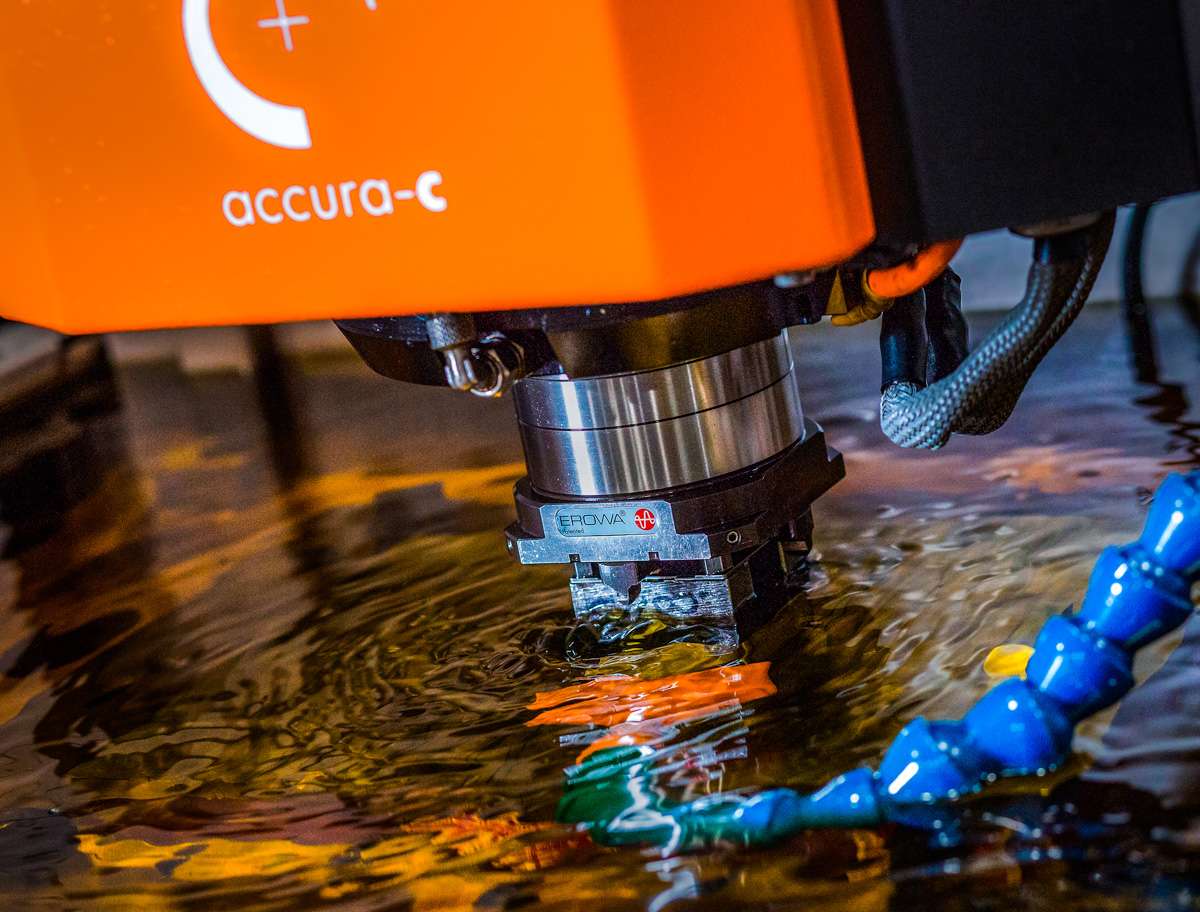
Please do not leave this page until complete. This can take a few moments.
Electron beams that meld layers of titanium. Powerful jets of water that slice through almost any material. The world’s largest 3D printer, which can print a 5,000-pound object in just three days. Five-axis routers that machine components to any degree of complexity. Manufacturing tolerances that are a fraction the size of a human hair.
These are just some of the capabilities of Maine companies that offer computer-aided precision technology, in a growing and evolving sector. They serve industries in Maine and around the world, ranging from aerospace to medical, energy, construction, transportation, defense and even the arts world.
In Biddeford, Form Tech Tool & Mold Inc. machines parts within tolerances that are 20 times less than the thickness of a human hair, says COO Kevin Kaserman.
The company makes molds for various industries, from micro-medical to large military applications. A mold (also called a “tool”) is a rigid frame used to make a product by filling it with a liquid or pliable material.
The computer-aided machines that make Form Tech’s customized molds can cost up to $500,000. They include an “electro discharge” machine (EDM) that uses an electric arc to burn away base material. The fully automated “lights out” machine can be programmed to work without human supervision 24/7 — and change its own tools as needed throughout the machining process.
“Before EDM, you might have needed 10 pieces to create a part,” says Mike Raymond, production manager. “Now we can use one piece of steel and create the shape we want.”
The technology simplifies the molding process and cuts production time.
“Twenty years ago, the normal lead time to build a large tool might have been half a year,” Raymond adds. “Today, we build that same tool in six to eight weeks.”
“It’s huge,” Manufacturers Association of Maine executive director Lisa Martin says of precision tech. “Of the 1,600 manufacturing companies in Maine, approximately 25% are precision fabrication facilities.”
The sector’s growth is tied to growth of industries, in Maine and beyond, such as aerospace, wood products and medical devices, she says.
Martin expects continued growth. “The sector is morphing, so more companies are using higher technology such as robotics,” she says. “The growth is in technology-based sectors such as medical devices, composites, electronics and metal fabrication.”
Machining technology has changed dramatically over the years, says John Bolduc, chairman of the precision and machining program at Southern Maine Community College.
“The machinery today is faster, more accurate and more consistent,” he says. “The cutting tool technology today is amazing. It can do multi-function, multi-axis machining. They can do ‘lights-out’ manufacturing: They load up the machines and run them overnight without supervision.”
The machines can cost up to $1 million.
“They’re taking a chunk of metal the size of a big truck tire and turning it into a turbine blade for a jet engine,” he says.
The sector is growing. A recent addition is Amplify Additive, a Scarborough start-up that became operational last year. It uses a type of additive manufacturing (commonly called 3D printing) that uses electron beams to fuse together successive layers of titanium powder in a vacuum to create medical implants. Temperatures reach more than 1,100 degrees Fahrenheit while the machine reads data from a 3D computer-aided design model. Parts are printed in 50-micron layers—about the same thickness of a human hair, says Amplify’s president and CEO, Brian McLaughlin.
Working on machines that each cost around $750,000, the process allows for the creation of geometrically complex parts that are lightweight and strong, and allows prototypes to be created as a single entity rather than in multiple parts.
The process moves quickly; from concept to final prototype takes about a week. For example, a total hip joint replacement involves implanting a hip cup that has hitherto been cast and then machine-coated afterward — a time-consuming process of perhaps six steps.
“We can just print the part with a 3D porous coating directly on the hip cup in a single step and then machine it,” he explains. “It’s two steps.”
At the University of Maine’s Advanced Structures and Composites Center, 3D printing is reaching new levels. Last fall, the center unveiled the largest 3D printer in the world. Made by Ingersoll Machine Tools in Rockford, Ill., the $2.5 million machine extrudes molten, paper-thin filament, at 500 pounds per hour, to produce objects up to 100 feet by 22 feet by 10 feet. To demonstrate its capabilities, the center printed a 25-foot, 5,000-pound boat, which took just three days. Although non-functional, it’s the largest 3D printed object in the world. Potential commercial uses include military, boatbuilding and energy applications.
Tolerances are within 1/6,000 of an inch, says Habib Dagher, the center’s executive director. In general, production time is cut from months to weeks.
“I don’t know of any other printer that has that capability,” he says.
The center is developing new software and hardware technologies to integrate with the printer. That includes high-performance computer connections for even faster and more precise printing, and artificial intelligence and sensor capabilities to make the printer “smart,” able to automatically adjust print patterns as needed, and able to produce “born certified” parts, meaning the end-product is ready for real-world use.
“We’re developing that technology as we speak,” says Dagher.
Westbrook-based Lanco Integrated makes robotic systems for clients to perform mass assembly and tests of their products.
“A lot of our customer base is medical,” says Mitch Sanborn, manager of manufacturing.
“We make robots that pick and place suture needles, thread the suture material into the needle, then package it. The fiber can be thirty-thousandths of an inch and it has to hit a hole in the needle that has a couple thousandths of an inch clearance,” he says.
The accuracy of these systems, depending on the client’s requirements, can get down to twenty-millionths of an inch. High-speed robots can pick up components and move them 6 inches for placement into the final assembly in less than 1 second while maintaining these accuracies.
Precision cutting machines include Trenton-based Nautilus Marine Fabrication Inc.’s Flow Waterjet. A powerful blast of water mixed with fine-grained sand and driven through a slim nozzle can cut flat stock — any kind of metal, stone, ceramic, plastic, composites, rubber, foam and wood — to almost any shape. The company caters mainly to boat builders looking for precision parts or odd shapes. The technology proved useful for a boat built by Brooklin Boat Yard to a design by architect Frank Gehry, who called for numerous lattice-styled cutouts in the hull and deck.
The water is blasted at 50,000 pounds of pressure per square inch. Three-quarters of a pound of sand runs through per minute, says the company’s president, Steve Brenton. The machine cuts to a thousandth of an inch. Nozzles, made from hard alloy, get used up quickly.
“It’s like having an acid that’s so strong it eats through anything, but you still have to contain it,” says Brenton.
He adds, “It will cut off your finger.”
Two large-format five-axis computer-controlled routers at Varney CNC in Brunswick offer faster set-up and cutting compared with traditional three-axis routers.
“Let’s say you have a 3-foot by 5-foot by 2-foot rectangle and you have to machine all sides of it,” says the company’s owner, Nathan Varney. “You can machine all five sides without ever having to flip the block over.”
The company caters to any industry that works with composites, including marine, aerospace, renewable energy, architectural and construction. Like the water jet cutter, the routers can cut to within a thousandth of an inch.
The high-tech machines themselves require special consideration, for things like temperature, humidity, cleanliness and rigorous calibration.
“You can’t just buy a 20-foot-long CNC [computer numerical control] router and plunk it down on the floor and start running,” says Varney. “You have to level the machine to at least the third or fourth decimal place.”
He adds, “There’s a lot of intricate set-up for this equipment. These aren’t your grandpa’s dirty machine shops anymore."
0 Comments