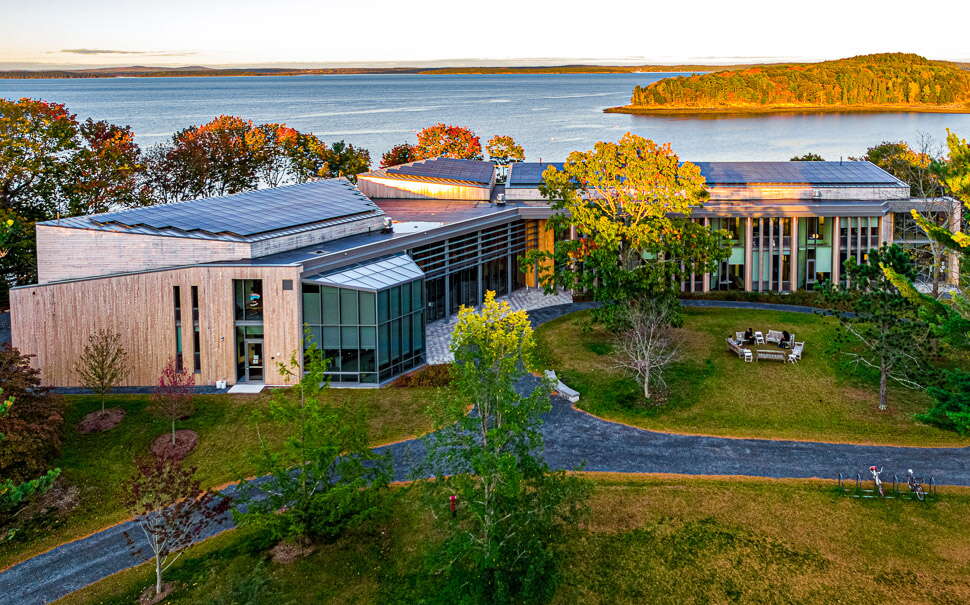
Please do not leave this page until complete. This can take a few moments.
Tears streamed down Joshua Henry’s face as he cited American novelist Jack London.
“I would rather be a superb meteor, every atom of me in magnificent glow, than a sleepy and permanent planet,” the chemist-turned-entrepreneur told the crowd at the July 2023 ribbon-cutting ceremony for TimberHP, the startup he co-founded six years earlier. “I shall not waste my days in trying to prolong them. I shall use my time.”
The bittersweet moment is captured in “The Comeback Mill,” Josh Gerritsen’s documentary film about how Henry joined forces with architect Matthew O’Malia to breathe new life into a defunct paper mill in the Somerset County town of Madison as the first U.S. manufacturer of high-performance wood-fiber insulation.
For the time being, however, the company’s fate rests with a bankruptcy judge in Delaware. The company started manufacturing in 2023 and added a second product in 2024, before financial difficulties stalled construction of a third product line. Currently operating with 54 employees, TimberHP filed a voluntary, pre-negotiated Chapter 11 reorganization plan in late March to lessen its debt.
The company’s road to recovery is far from certain — and could be as bumpy as the start.
The closure of Madison Paper Industries in May 2016 marked the end of an era for the 4,800-population Kennebec River town, which had been home to a paper mill since 1899. It was Maine’s fifth major paper mill to close in three years, leaving 214 people without jobs and a 600,000-square foot factory empty.
Two years later, Henry and O’Malia bought the building with the goal of manufacturing wood fiber insulation — an environmentally friendly material used for 20 years in Europe where the market has grown close to $800 million.
Timber HP began production in 2023, using wood chips and thinnings left over from timber harvesting to make fire- and sound-resistant thermal insulation that arrives at construction sites with a negative carbon footprint. The company added a second production line in February 2024.
Early customers included the College of the Atlantic in Bar Harbor, which used the company’s TimberBatt insulation to build the $20 million Davis Center for Human Ecology completed in 2021. More recently, the college used TimberBatt in the construction of the Collins House, a 46-bed residence hall that opened in 2024.
“We were really attracted to the product because of the regional sustainability angle,” says school spokesman Rob Levin. “It works just as well as any other high-value insulation product.” He notes that using a carbon-neutral alternative to fiberglass aligns with the school’s goal of becoming a fossil fuel-free campus by 2030.
In Westbrook, the Seavey Terraces Apartment Complex completed in 2024 — and leased by the University of New England for student housing – was the first residential development constructed with TimberHP’s loose fill and dense pack insulation branded as TimberFill.
Developer Jack Soley says that while the original intention had been to use cellulose, TimberHP matched the price which made it a “no brainer” to use a greener alternative.
“I don’t know what the price would have been, but we certainly couldn’t have gotten it from Europe — we couldn’t have afforded it,” he says.
If and when TimberHP comes out with a planned wood fiber board product, Soley says he would be interested in using that in workforce housing construction. He’s developing projects in partnership with Avesta Housing and Hebert Construction CEO Tim Hebert through a venture called Domus.
“Right now we all use a plastic insulation board that’s petroleum-based and horrible for the environment,” Soley says. “If they [TimberHP] can produce a wood-fiber board that performs equally in terms of insulation quality, then a lot of folks like myself would pay a little bit extra to do the right thing.”
TimberHP does indeed plan to make a product called TimberBoard, which it is banking on to become its biggest revenue and profit generator. However, those plans remain stalled by unbudgeted cost increases and $30 million in construction cost overruns.
In legal filings, TimberHP blames inflation and pandemic-related supply chain constraints for the spike in expenses, particularly the price of steel and electrical components. The company also mentioned unexpected engineering problems associated with retrofitting the mill that resulted in substantial change orders. Court filings show that Cianbro Corp., Maine’s largest construction firm, is still owed $15 million for its work on the project. It would get only 53% of that amount according to the restructuring plan that still requires judicial approval.
Asked whether the Pittsfield-based company supports the plan, Cianbro spokeswoman Shelby Hartin says, “We want TimberHP to come out of this successfully and vibrantly. We’re doing what we can to protect our interest and theirs.”
Between 2019 and 2024, TimberHP raised equity and took on millions in debt to finance the purchase and redevelopment of the Madison property, buy equipment and fund operations.
On the equity side, the company raised an initial $40 million in 2021. But its attempt in 2023 to raise another $60 million to complete construction of the factory with a third production line fell far short of the target, bringing in only $31 million.
The company also enlisted lending help from public entities including $400,000 from the town of Madison, $3.5 million from the Maine Venture Fund that was never converted into equity as per the arrangement; and from the Finance Authority of Maine.
FAME also arranged the 2021 sale of $85 million in tax-free bonds to 14 institutional investors that manage large municipal bond funds. TimberHP used the proceeds to finance construction of its manufacturing facility. The restructuring plan anticipates bondholders who choose not to participate in the restructuring plan will get 2% of their money back but leaves a blank for the anticipated recovery for those who choose to participate.
Maine Technology Institute provided close to $2 million in grant funding and $200,000 in loans, of which $22,705 was paid back before the bankruptcy filing, according to MTI President Brian Whitney. MTI is “hopeful” of the reorganization plan succeeding, he says. Whitney declined to comment on whether MTI supports the debt relief and reinvestment plan outlined in the Chapter 11 filing.
In all, Timber HP “borrowed a lot of money from a lot of different sources, including a lot of government-financed lending,” says Roger Clement, a partner with the Portland-based law firm Verrill who reviewed the case filings for Mainebiz. “This is the classic example of the entrepreneur who raises money to build a bridge and runs out of money before the bridge hits the other shore.”
Saddled with rising costs and debt, TimberHP tried in vain to sell the company. After a potential suitor backed out in February, the owners pursued a restructuring plan — backed by more than 25 creditors — to slice $100 million in debt from its books and reemerge with a new business plan. The amount of TimberHP’s total indebtness was not immediately clear from the filings.
In early March, after TimberHP’s attempt to find a buyer for the business fell through, FAME’s board approved $7 million in commercial insurance associated with a $10 million loan from BlackRock for the company. FAME spokesman Bill Norbert says the loan insurance was authorized amid hope that TimberHP will emerge as a more robust company.
“Everyone is rooting for this mill to succeed,” Norbert says. “It’s so important for the area, the jobs at the mill, in Madison and the surrounding area, and all the indirect benefits to local businesses such as wood suppliers and vendors … We never like to see a company go bankrupt.”
Mark Williams, a finance lecturer at Boston University’s Questrom School of Business, cautions that ramping up in a time of economic turmoil could be a risky move for TimberHP.
“There’s a high probability that we’re going to be moving into recession, which is obviously not the best time” to come out of a Chapter 11 reorganization, he says.
TimberHP says it has $29 million in fresh financing. O’Malia referred all requests for comment to Delaware-based lawyer Mark Felger at Cozen O’Connor, the firm representing the company in the bankruptcy case. Felger did not return phone calls before this article went to press.
TimberHP’s gross revenues in 2024 were around $4.7 million. Once it gets back on its feet, it is projecting net revenues of $15.7 million between July and December 2025 and then $101.9 million in 2026. The company aims to return to profitability in
2026.
When completed, the Madison facility will have the capacity to generate up to $170 million in sales, or about 2% of the U.S. residential and commercial insulation markets, according to the case filings.
If the company achieves that goal, “that’s a massive amount of insulation,” says developer Jack Soley. He drives past the TimberHP factory a couple times a year and remains hopeful that the company will be able to close the chapter on Chapter 11 and get back on track to profitability.
“If they do go bust, then I’m just back to plastic wallboard insulation or spray foam,” Soley says.
Either ending would make for a compelling follow-up to Gerritsen’s 23-minute film about TimberHP, which fades out with an aerial view of the mill adjacent to the rushing Kennebec River below a gray, cloudy sky: “It’s a film about possibility,” he says.
Gerritsen wants the film to inspire other communities to revitalize neglected infrastructure. He doesn’t plan a sequel — that’s up to TimberHP and the bankruptcy court.
0 Comments