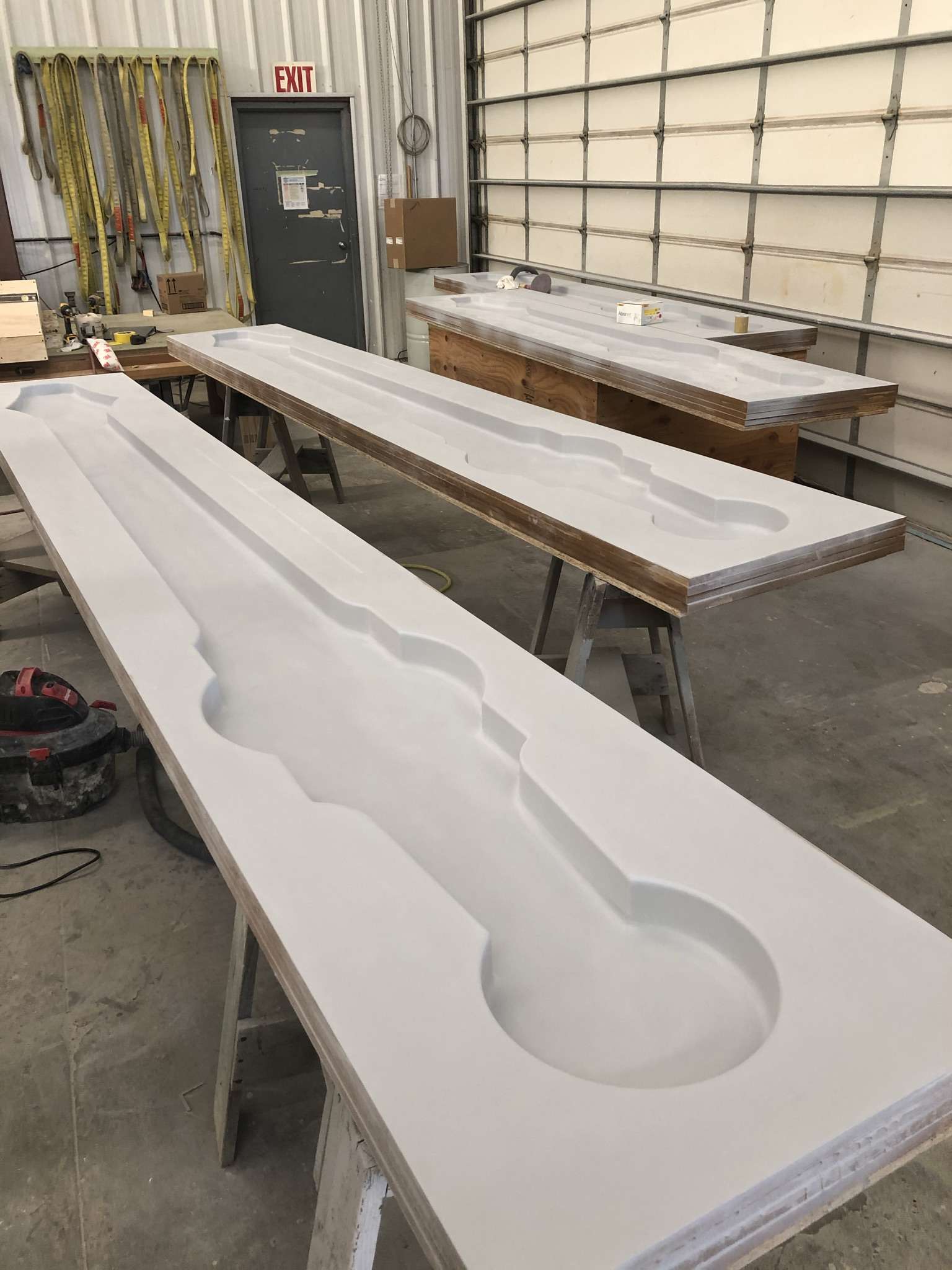
Please do not leave this page until complete. This can take a few moments.
Lyman-Morse Technologies combined its custom composite capabilities with precision fabrication technology to create historically accurate clock hands for Boston’s landmark Custom House Tower.
The firm is a division of Lyman-Morse Boatbuilding in Thomaston.
It was contracted by Knollmeyer Construction Corp. in September to build five sets of clock hands by December, according to a news release.
The four-side clock is part of the large tower atop the Financial District’s Custom House building, whose original structure dates to 1847.
The 495-foot tower and clock were added to the building in 1915-16. For years it was Boston's tallest building, before it was surpassed by the Prudential Tower in 1964.
The contract was to build four sets of minute and hour hands for the four clock faces, plus a spare set.
Requirements included weight restrictions, stiffness and weather-resistance. It also needed to be historically accurate, requiring a Boston Landmark Commission-approved gold finish.
The original hands were made from birch, but were rebuilt in fiberglass in the 1980s, Andy Smith, vice president of Lyman-Morse Technologies, told Mainebiz.
After the firm was selected for the job, a team from Knollmeyer visited, bringing birch and fiberglass hands with them.
The fiberglass laminate had started to deteriorate and the hands were becoming waterlogged, he explained.
“When you’ve got a 13-foot hands and it starts to get waterlogged, it adds a lot of strain to the mechanism,” he said. “The clock would periodically give up and say, ‘I can’t do this anymore.’”
The goals were to reduce the weight of the hands and make them watertight.
“We do that well because we’re a boatbuilder,” Smith said.
The 1980s job had deviated from the original design.
“We reverted back to the original early 1900s design for the geometry,” Smith said. “Ours are more historically correct than the last set.”
It was also essential to get the interfaces right with the existing clock mechanism, he said. “There was a lot of detail that needed to be just right."
For example, the minute hand fits onto a slightly tapered shaft on the old clock mechanism.
“So we had to match the tapered shaft to the hub that we made to fit into the minute hand,” he said.
The precisely fabricated hub allows the minute hand to slide onto the clock mechanism; it’s then secured in place.
The hour hand had a component fitted with a thread dating back to the early 1900s.
“It’s a thread that doesn’t exist anymore. So instead of changing that, we used the old hardware from the hour hand and fitted it onto our hour hand so that we didn’t have to worry about cutting a thread that was obsolete.”
The hands were made from carbon fiber laminates infused with epoxy resin, which has a strength-to-weight ratio that’s much better than fiberglass, according to Smith. The materials and process for making the hands were much like those used for boatbuilding. It involved making 3D drawings in a computer-aided design program, using specifications from the original birch hands.
The drawings were used to program a computer numerical control cutting machine to cut molds for the hands. The machine has a cutting tolerance of just a few thousandths of an inch, Smith said.
Carbon fiber cloth is layered into the molds and resin is infused into the carbon fiber using a vacuum bagging process. Due to the tight production window, two sets of molds were created to speed up the production process.
The hands were delivered December 10.
Lyman-Morse Boatbuilding President Drew Lyman, a Mainebiz NEXT List honoree, has previously said that innovation and diversification are key to keeping pace in an industry vulnerable to economic ups and downs. The company has invested in a computer numerical control machine, plasma cutter and 3D printer and balances its boat-related operations with work outside the boating industry, through Lyman-Morse Technologies, Lyman-Morse Fabrication, and Wayfarer Marine in Camden.
The Giving Guide helps nonprofits have the opportunity to showcase and differentiate their organizations so that businesses better understand how they can contribute to a nonprofit’s mission and work.
Learn MoreWork for ME is a workforce development tool to help Maine’s employers target Maine’s emerging workforce. Work for ME highlights each industry, its impact on Maine’s economy, the jobs available to entry-level workers, the training and education needed to get a career started.
Learn MoreWhether you’re a developer, financer, architect, or industry enthusiast, Groundbreaking Maine is crafted to be your go-to source for valuable insights in Maine’s real estate and construction community.
Coming June 2025
Learn moreThe Giving Guide helps nonprofits have the opportunity to showcase and differentiate their organizations so that businesses better understand how they can contribute to a nonprofit’s mission and work.
Work for ME is a workforce development tool to help Maine’s employers target Maine’s emerging workforce. Work for ME highlights each industry, its impact on Maine’s economy, the jobs available to entry-level workers, the training and education needed to get a career started.
Whether you’re a developer, financer, architect, or industry enthusiast, Groundbreaking Maine is crafted to be your go-to source for valuable insights in Maine’s real estate and construction community.
Coming June 2025
In order to use this feature, we need some information from you. You can also login or register for a free account.
By clicking submit you are agreeing to our cookie usage and Privacy Policy
Already have an account? Login
Already have an account? Login
Want to create an account? Register
In order to use this feature, we need some information from you. You can also login or register for a free account.
By clicking submit you are agreeing to our cookie usage and Privacy Policy
Already have an account? Login
Already have an account? Login
Want to create an account? Register
This website uses cookies to ensure you get the best experience on our website. Our privacy policy
To ensure the best experience on our website, articles cannot be read without allowing cookies. Please allow cookies to continue reading. Our privacy policy
0 Comments