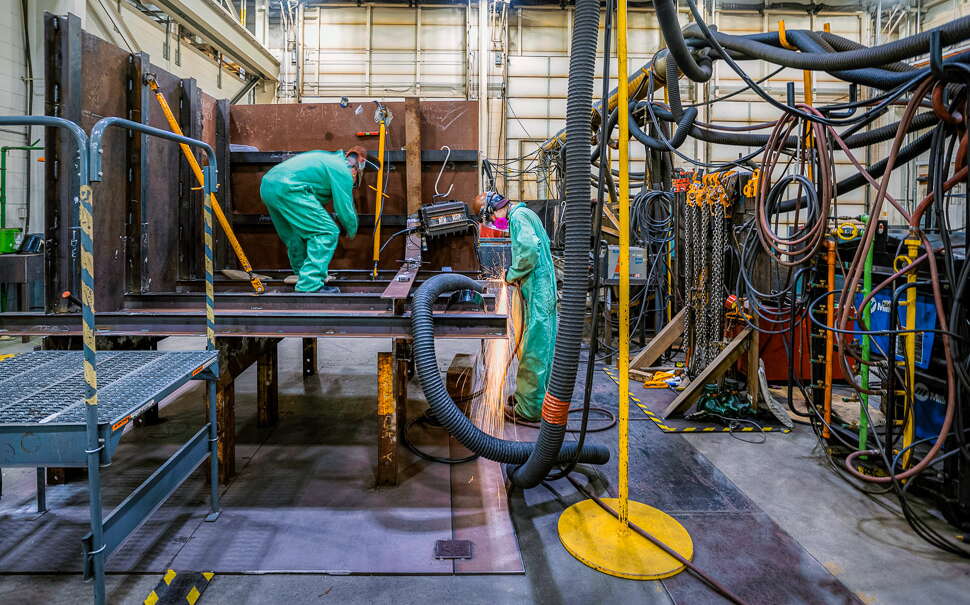
Please do not leave this page until complete. This can take a few moments.
This fall Deliah Schreiber graduated from an apprenticeship program offered by Bath Iron Works, a General Dynamics-owned shipyard with 6,500 employees and a ongoing demand for new workers.
The four-year program required four days per week on the job and one day in the classroom, providing wages, benefits and advancement opportunities from the get-go, a debt-free associate’s degree upon completion and the chance to pursue bachelor’s and master’s degrees.
Schreiber (who is not related to this writer) started her apprenticeship with no construction experience.
Today, she’s an inside machinist with “super seniority,” meaning she has first dibs on further training and gets a raise every thousand hours of work.
“I’ve definitely learned a lot of skills that I wouldn’t have learned had I not taken this route,” she says.
The apprenticeship program is just one of a slew of initiatives BIW has underway to attract and retain workers.
The shipyard invested $11 million in recruiting new workers between 2016 and 2023, and over the past five years spent $90 million on training — more than twice what was spent on training in the prior five years.
“Bath Iron Works’ ability to be a major driver in the state’s manufacturing economy depends on attracting, training and retaining the workers who make ‘Bath built’ best built,” Charles Krugh, BIW’s president, has said.
Krugh said BIW’s entry-level jobs have the potential to lead to “significant earnings and professional growth over time.”
Since 1950, the BIW Apprentice School has produced over 1,200 graduates. Apprentices earn while they learn about shipbuilding trades, marine design and production planning. The program combines academic and on-the-job training that, upon completion, provides an associate of science degree, which can lead to a bachelor’s or master’s degree.
Apprentices receive a certificate of apprenticeship from the state. Premium pay is given for overtime. Additional benefits include paid vacation, paid holidays, pension plans, medical plans, life insurance, workers’ compensation, unemployment insurance and Social Security benefits. Wages follow a pay progression.
“I was an apprentice when I started here in 1988,” says Tom Stevens, BIW’s director of training who oversees the workforce pipeline programs.
Then, the program enrolled about 20 people per year.
“We decided to increase that,” says Stevens. “This school year, we were able to get 66 apprentices. We’re recruiting for next year for another 100 through every pot we can. And we want to continue to hire 100 each year.”
Apprentices this year range from 18 to 50-something and hail from across Maine. Some are just starting their professional lives, others are looking for a career change.
A Maine native who lives 25 minutes from Bath, in Lisbon, Schreiber was familiar with BIW through her dad, who works there and went through the apprenticeship program himself about 10 years ago.
Schreiber, now 26, was in college when the pandemic hit and decided to pivot.
“I reached out to the director of the apprenticeship program,” she says. “I figured it was a good time to join the workforce.”
She liked the idea of on-the-job training combined with class work, with no prior experience needed.
“Before that, I had never really read a tape measure,” she adds.
Uncertain whether she wanted to pursue welding or machining, she first enrolled in a three-week paid training course held at Southern Maine Community College in partnership with BIW, that offers an overview of skills like blueprint reading, tool work and safety.
That helped her decide on machining, so she started her apprenticeship in November 2020. She was immediately assigned to a mentor, starting on a hydraulic side press.
“Once I was proficient and comfortable enough to run it, I moved to a new machine and so on,” she says.
Four years in, she enjoys the challenge. “I learn something new every day,” she says.
Other pipelines are new. “We’ve been trying to crack the code of how to get into the schools and change the mindsets that not every kid is going to become a doctor and go to college,” says Stevens.
Recent efforts include partnering with Jobs for Maine Graduates, an education nonprofit that partners with public education and private businesses to help students achieve their career goals.
A two-year rotational professional development program prepares high-potential individuals for leadership roles. Participants are individually mentored by leaders and complete rotations that cover critical aspects of the shipbuilding process, working in a wide variety of roles.
Candidates for the summer internship program are selected from maritime and academic institutions for positions including engineering, design, finance, planning and scheduling, materials and quality, manufacturing operations, safety, HR and labor relations.
A partnership with the Maine Community College System and Maine Quality Centers offers pre-hire workforce training free to qualified applicants, targeting specific jobs such as welding, manufacturing and marine design. Graduates receive an interview with BIW.
The partnership, established seven years ago, has resulted in a 93% retention rate.
“We just had a graduation the other night,” says Stevens. “We celebrated our 81st class.”
In an effort to increase the number of veterans hired, BIW partnered with the U.S. Department of Defense Skillbridge program, an internship program which connects transitioning service members to training opportunities; Maine’s Hire-A-Vet Campaign; and Boots2Roots, a Portland-based nonprofit that prepares active-duty military members for their transition to the civilian workforce.
The BIW Training Academy is in a 32,000-square-foot facility at Brunswick Landing. Training simulations mimic real-world jobs and scenarios, and promote teamwork, engaged learning and problem-solving for skills required to work safely in the shipyard and manufacturing environment.
The BIW Training Trailer program started in June 2023. A custom-built 53-foot trailer can be configured for various purposes and brought to external locations to support hiring, training and other BIW programs.
With power, wi-fi and heat and air conditioning, job candidates and new hires can complete hiring applications as well as learn and practice trades-based skills classes using advanced technology including virtual reality. BIW’s training team can bring both hands-on and virtual training to all parts of Maine as well as across New England and beyond as a standalone center of learning.
The trailer has visited high schools, fairs, festivals, community colleges, career and technical education events — even the balloon festival in Lewiston.
“We’ll configure it to promote what BIW does and show the opportunities people have to work for us,” says Stevens.
So far, the program has connected with over 4,000 people across Maine.
New this year is an eight-week training program that launched with 15 students at Wiscasset High School. It’s early yet to assess outcomes, but things are looking good.
“So far we’ve been seeing great results,” says Stevens. “The kids are excited to see us.”
BIW is looking to roll out a feeder program with community and technical education programs next year. The company recently hosted a roundtable with CTE and community college leaders, BIW, Texas-based nonprofit BlueForge Alliance and other outfits to discuss creating a curriculum at CTE schools specifically geared to jobs with Maine’s defense contractors. Follow-up meetings are expected.
“We’re trying to offer a lot of pathways to the shipyard,” says Stevens.
There are other obstacles to recruitment. For one, affordable housing would be welcome, says Garrett Brown.
Brown started in the apprentice program in 2019 and is now a deck-plate planner. He commuted 25 miles from Gardiner for four years before finding a place a few minutes away in Bath.
But his living situation is uncertain. He and a friend are splitting the rent for a short-term apartment. The average person feels priced out, the 26-year-old says.
“The concern is, every time the lease comes up, my friend says, What’s our plan?” Brown says. “We have it until end of February right now.”
BIW’s ability to hire will depend on workers being able to get access to child care, transportation and affordable housing and education, according to a recent economic analysis.
Earlier this year, BIW said initiatives to be supported by U.S. Navy funding of more than $34 million will include funding 85 new housing units for BIW workers closer to the shipyard, providing 150 additional year-round child care slots for BIW workers and providing free bus services for BIW employees in the Bath and Brunswick areas.
There’s been progress on the childcare front. BIW and the Bath Area Family YMCA announced a partnership to expand access to childcare for midcoast families. That will include 150 spaces to the children of BIW employees across two YMCA centers in Bath and Brunswick.
To accommodate the expansion in the organization’s childcare program, the YMCA bought a property in Brunswick to renovate into a 10-classroom childhood education center. Enrollment is expected to begin in January for a target opening of September 2025.
Last year, BIW began working with Western Maine Transportation Services in Auburn to expand commuter bus transportation between Lewiston and Bath.
Key to the initiatives are collaborations with Maine businesses, including others in the shipbuilding industry, on support for workforce housing, childcare and transportation through direct investment, tax credits and other incentives, the company said.
“We are working closely with community groups, the U.S. Navy and our congressional delegation to overcome some of the current challenges to workforce participation,” Krugh said. “At the same time, we are investing in important quality-of-life improvements and modernization in the workplace to attract, retain and provide long-term opportunity to the men and women who are essential to the nation’s critical shipbuilding capacity.”
0 Comments