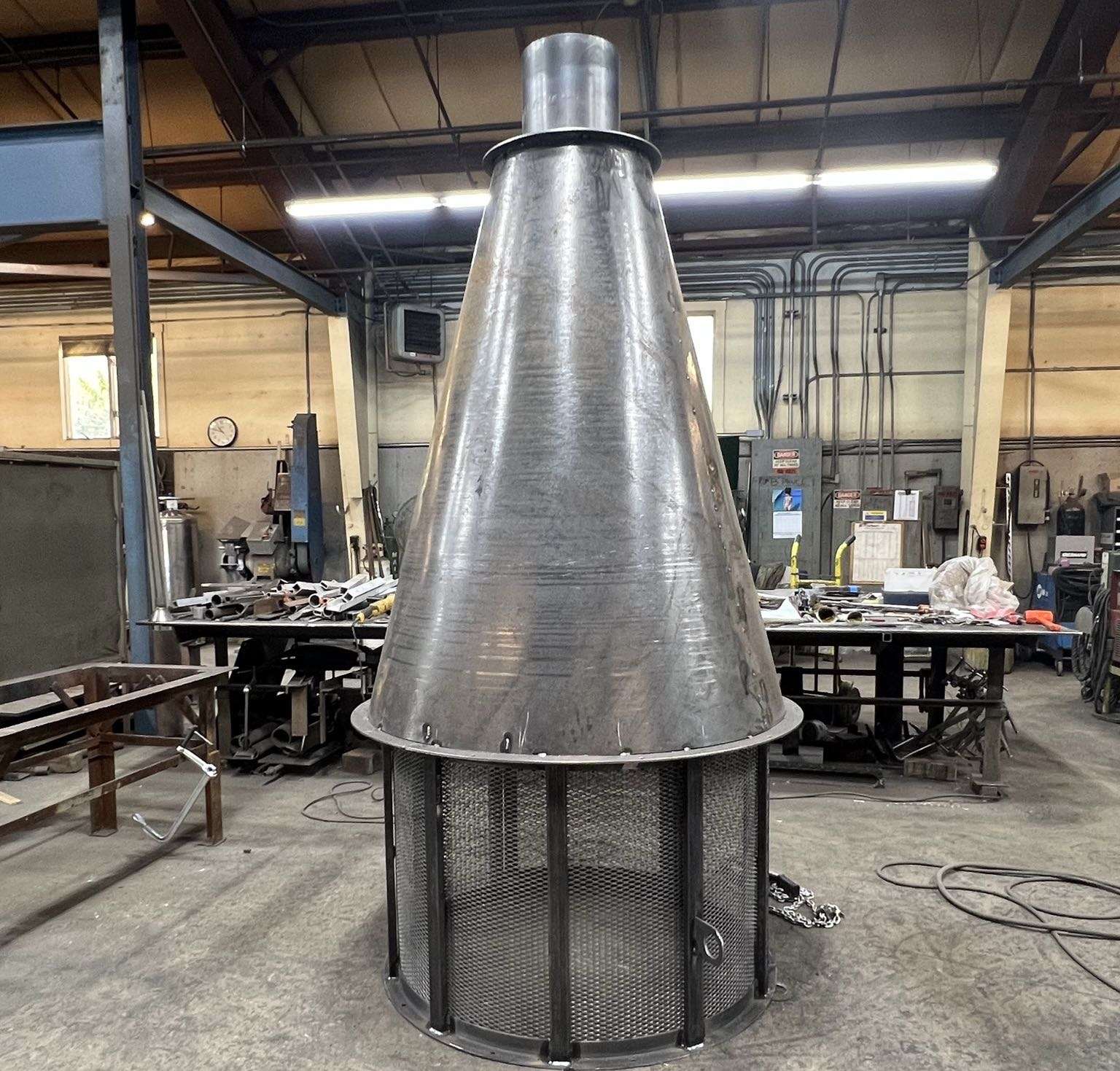
Please do not leave this page until complete. This can take a few moments.
A fabrication facility in Brewer was awarded $260,000 in federal grant money to help it buy a new high-tech cutting machine — a purchase that’s expected to increase revenue growth by 10%.
Troy Industrial Solutions received the money from Maine Technology Institute’s Pandemic Recovery for an Innovative Maine Economy Fund, which aims to distribute $39 million in federal funding to help Maine businesses recover from the harm caused by the pandemic via business development and innovation in technology.
The amount granted to TIS was part of the first phase of the fund, which targets small businesses across Maine that work in, use or leverage solutions connected to Maine’s technology sectors.
Founded in 1862 and headquartered in Watervliet, N.Y., Troy has operations in Brewer, New Hampshire and Connecticut. It provides electro-mechanical equipment diagnostics, repair, replacement, transportation, installation and training services to manufacturing, aggregate, agricultural, power generation, municipal and industrial clients throughout the Northeast.
The Brewer location is a fabrication facility and service shop. A recent project was the design and fabrication of a baghouse, which is an industrial dust collector, along with an associated stack and screw conveyor for a soil remediation company in New Hampshire.
David Barcomb, Troy’s senior business advisor, told Mainebiz that Troy’s presence in Brewer resulted from an acquisition of Lane Conveyors and Drivers in November 2015. Lane had been at the Brewer location for nearly 60 years. With the deal, about 40 of Lane’s employees agreed to be hired by Troy.
Today, the location has 38 full-time employees.
The Brewer plant has a 25,000-square-foot footprint consisting of three industrial buildings — an office and warehouse building, the main fabrication shop and a machine shop that also accommodates walk-in trade for metal fabrication.
Products made in Brewer go to customers throughout the Northeast, from northern New Jersey to Syracuse N.Y., and across New England.
Since the 2015 acquisition, Troy has invested close to $750,000 in the Brewer facility.
“We completely renovated the office space to make the work environment much more attractive, to bring in new talent,” said Barcomb. “We’ve invested in software and hardware equipment to improve the drafting and design teams’ resources. We bought machine tools and metal fabrication equipment. So we’ve made a substantial investment into the Brewer facility.”
This year, Troy brought in three new pieces of “mini-fab” equipment at a total cost of about $150,000.
With the $260,000 grant and Troy’s matching funds, the company can now move forward with plans that were put on hold as a result of the pandemic.
In order to improve the quality of its products and stay in a competitive position in the market, it was determined that the company needed to replace a 20-year-old plasma table that is obsolete in both hardware and software.
Troy is in the process of sourcing a new five-axis computer numerical control high-definition plasma table to purchase that would provide premium cutting performance.
The cost of the new plasma table is expected to be over $500,000.
“We submitted the grant with a $520,000 budget. It’s a dollar-for-dollar match,” said Barcomb.
In November, the team plans to travel to Atlanta to an annual FabTech trade show to identify which model it wants.
The five-axis table will replace a two-axis table that’s equipped with older software and limitations with regard to factors such as tolerances and cutting angles.
The five-axis device will be able to make much cleaner and more precise cuts, and will allow the company to eliminate the manual rework it currently has to do in order to meet customers’ precision specifications.
“Our expectation is that we’ll be gaining efficiency by eliminating rework,” he said. “And it will open up the opportunity to take on additional types of businesses that we can’t do currently.”
In addition to investing in new processing equipment, Troy will be using the funds to hire additional employees to support the investment, including a CNC operator, fabricator and welder.
Based on efficiencies gained with the purchase of the new equipment, Troy said it anticipates growth in revenue of 10% over current estimates.
And the additional growth in revenue is expected to allow Troy to move forward with other growth strategies. The next phase of the plan includes incorporating a 5,000-square-foot high-bay addition onto the existing fabrication facility, thus allowing Troy to handle larger projects and provide additional skilled manufacturing job opportunities.
“Right now, we have some limitations with regard to lifting capacity and pick height,” said Barcomb. “We’ve started to explore e a 5,000-square-foot high-bay addition to our main fabrication building. That’s probably at least two years out.”
Barcomb credited the Brewer Economic Development Office for introducing it to the MTI program.
“The state of Maine has been very helpful to us in growing ad investing in our business in Brewer. It’s been pleasure working up there,” he added.
The Giving Guide helps nonprofits have the opportunity to showcase and differentiate their organizations so that businesses better understand how they can contribute to a nonprofit’s mission and work.
Learn MoreWork for ME is a workforce development tool to help Maine’s employers target Maine’s emerging workforce. Work for ME highlights each industry, its impact on Maine’s economy, the jobs available to entry-level workers, the training and education needed to get a career started.
Learn MoreWhether you’re a developer, financer, architect, or industry enthusiast, Groundbreaking Maine is crafted to be your go-to source for valuable insights in Maine’s real estate and construction community.
Coming June 2025
Learn moreThe Giving Guide helps nonprofits have the opportunity to showcase and differentiate their organizations so that businesses better understand how they can contribute to a nonprofit’s mission and work.
Work for ME is a workforce development tool to help Maine’s employers target Maine’s emerging workforce. Work for ME highlights each industry, its impact on Maine’s economy, the jobs available to entry-level workers, the training and education needed to get a career started.
Whether you’re a developer, financer, architect, or industry enthusiast, Groundbreaking Maine is crafted to be your go-to source for valuable insights in Maine’s real estate and construction community.
Coming June 2025
In order to use this feature, we need some information from you. You can also login or register for a free account.
By clicking submit you are agreeing to our cookie usage and Privacy Policy
Already have an account? Login
Already have an account? Login
Want to create an account? Register
In order to use this feature, we need some information from you. You can also login or register for a free account.
By clicking submit you are agreeing to our cookie usage and Privacy Policy
Already have an account? Login
Already have an account? Login
Want to create an account? Register
This website uses cookies to ensure you get the best experience on our website. Our privacy policy
To ensure the best experience on our website, articles cannot be read without allowing cookies. Please allow cookies to continue reading. Our privacy policy
0 Comments