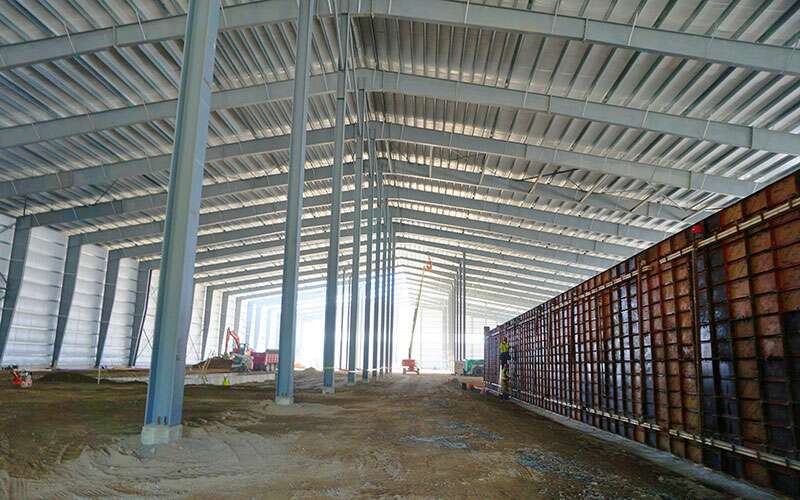
Please do not leave this page until complete. This can take a few moments.
HAMPDEN — Work on the $70 million Fiberight waste-to-energy plant is progressing after its scheduled opening in April was delayed, and company officials want to make sure the municipalities involved stay up to date with the process.
Monday, officials from member communities were invited to tour of the 144,000-square-foot plant, something that will be a monthly event as a way of keeping people up to date, CEO Craig Stuart-Paul said Monday to media, who also were invited to tour the plant.
The company Monday also announced new recycling initiatives involving textiles, paper and glass, that were spurred by changes in the recycling market.
The plant was scheduled to open in April to accommodate municipalities that had been sending waste to the Penobscot Energy Recovery Corp. incinerator in Orrington. The contract between those communities and PERC expired in March.
Winter weather and other issues delayed Fiberight construction, however, and much of the trash that would have gone to Fiberight is going to landfills, including the Crossroads landfill in Norridgewock, until the plant is open.
Stuart-Paul said Monday that Fiberight wants to be as transparent as possible with members during the construction process, including the monthly tours for officials and the media.
“The best thing to do is what we’re doing,” he said. “Make sure the community is here every month.
“Sunshine is the best disinfectant,” he added.
He said Hampden officials are welcome onsite any time.
The weather was the latest issue in a sometimes rocky process that began in 2012, when the 187-member Municipal Review Committee began looking for options after the 17-year contract with PERC ended. MRC settled on Fiberight, but it was a tough sell to many of the member communities, some of which were sceptical of Fiberight’s technology and its ability to recycle as much waste as it said it would.
About half of the MRC communities, as well as some not in MRC, signed on to make up the 115 customers the plant now has.
Legal challenges and financing hurdles also slowed plans.
Recycling is scheduled to begin at the plant in late September, and the company will start slow, so it can gauge the waste stream. By the end of the year, the plant will be fully operational, including converting organic waste into biofuel and refined bioproducts in a massive anaerobic distiller next to the building, which is being shipped from Holland.
Once it’s fully functional, 115 customers will send as much as 180,000 tons of waste a year to the plant, which uses a high-tech process to sort, recycling, reuse and refine the waste.
The process has been tested in the Maryland-based company’s Virginia prototype plant for several years, but the Hampden facility will be by far the largest use of the technology, Stuart-Paul said.
In simple terms, the process starts when rubbish bags are shredded by a machine, and the waste then goes through a series of screens, which separate and channel different sizes and types.
Eventually the organic waste goes into a pulper that breaks down the organic material, forming a biomass and removing contaminants, then removing remaining recyclables, like metals. The pulp is eventually converted to fuel in the anaerobic digester.
Fiberight estimates is will make use of 80% of the waste that’s brought to the plant, a much higher figure than the average for the municipal waste stream.
In 2014, the most recent year Environmental Protection Agency figures are available, Americans generated 258.5 million tons of municipal solid waste; of that, 136 million tons went into landfills, meaning less than half was recycled or converted. The average American generated 4.4 pounds of trash a day in 2014, up from 2.68 pounds in 1960.
“We’re not just bringing stuff in and sorting,” Stuart-Paul said Monday. “It all gets processed.”
The building also has an odor control system that pulls air through the building, and plans are to install the duct work for that once the concrete floor is down.
He pointed out the tipping platform isn’t that large. “We want to process what comes in as fast as we can,” he said. “It doesn’t do any good to have organic waste lying around.”
Stuart-Paul said it will take some time to get to know the waste stream and make sure processing is efficient.
The floor of the new Fiberight building, which is now a giant shell, are still dirt, but the forms for the concrete tipping platform are being poured and Stuart-Paul said the digester, pulper and other essential parts are due in the coming weeks.
The anaerobic digester will be outside, in a spot now empty and marked with stakes. The pulper and 600,000-gallon washing system will come into the building through the roof, then the roof will be completed.
Recent market changes for recycled materials have spurred new possibilities at Fiberight, officials said Monday in a news release before the tour.
The cost of recycling mixed paper has increased, forcing many communities to landfill or incinerate it rather than recycle. Director of Community Services, Shelby Wright said, “Fiberight’s technology may be able to reverse this trend by providing a domestic solution for mixed paper and we are looking at ways to advance this solution for our member communities.”
The company also announced a partnership with New Hampshire-based Apparel Impact, which will put collection boxes through the region to collect clothes, shoes, bedding, and other fabric-based goods though would otherwise likely go to a landfill.
Wright said the Hampden plant will “form an important part of a textile recycling network by acting as a collection center for smaller communities,”
The company will work with member communities that don’t have the volume to support a collection box, allowing them to send small quantities of separated textiles in larger loads that are already going to the plant.
She said more than dozen communities say they’re interested in the new program and the collection boxes have already been placed in some towns, including China and Vassalboro.
Stuart-Paul said the company is also looking into developing a regional glass processing plant on site as the cost of glass recycling rises in Maine.
He said that most of the state’s recyclable glass, about 40,000 tons a year, had gone to Massachusetts, but because of plant closures, it’s now going farther away, making recycling it more expensive.
“As a result, we have discovered that source separated glass bottles are being landfilled,” he said, adding that while there are still some details to work out, things are on track and everyone has their eye on the end result. “The whole idea is to use as much of the waste stream as possible.”
The Giving Guide helps nonprofits have the opportunity to showcase and differentiate their organizations so that businesses better understand how they can contribute to a nonprofit’s mission and work.
Learn MoreWork for ME is a workforce development tool to help Maine’s employers target Maine’s emerging workforce. Work for ME highlights each industry, its impact on Maine’s economy, the jobs available to entry-level workers, the training and education needed to get a career started.
Learn MoreWhether you’re a developer, financer, architect, or industry enthusiast, Groundbreaking Maine is crafted to be your go-to source for valuable insights in Maine’s real estate and construction community.
Coming June 2025
Learn moreThe Giving Guide helps nonprofits have the opportunity to showcase and differentiate their organizations so that businesses better understand how they can contribute to a nonprofit’s mission and work.
Work for ME is a workforce development tool to help Maine’s employers target Maine’s emerging workforce. Work for ME highlights each industry, its impact on Maine’s economy, the jobs available to entry-level workers, the training and education needed to get a career started.
Whether you’re a developer, financer, architect, or industry enthusiast, Groundbreaking Maine is crafted to be your go-to source for valuable insights in Maine’s real estate and construction community.
Coming June 2025
In order to use this feature, we need some information from you. You can also login or register for a free account.
By clicking submit you are agreeing to our cookie usage and Privacy Policy
Already have an account? Login
Already have an account? Login
Want to create an account? Register
In order to use this feature, we need some information from you. You can also login or register for a free account.
By clicking submit you are agreeing to our cookie usage and Privacy Policy
Already have an account? Login
Already have an account? Login
Want to create an account? Register
This website uses cookies to ensure you get the best experience on our website. Our privacy policy
To ensure the best experience on our website, articles cannot be read without allowing cookies. Please allow cookies to continue reading. Our privacy policy
Comments