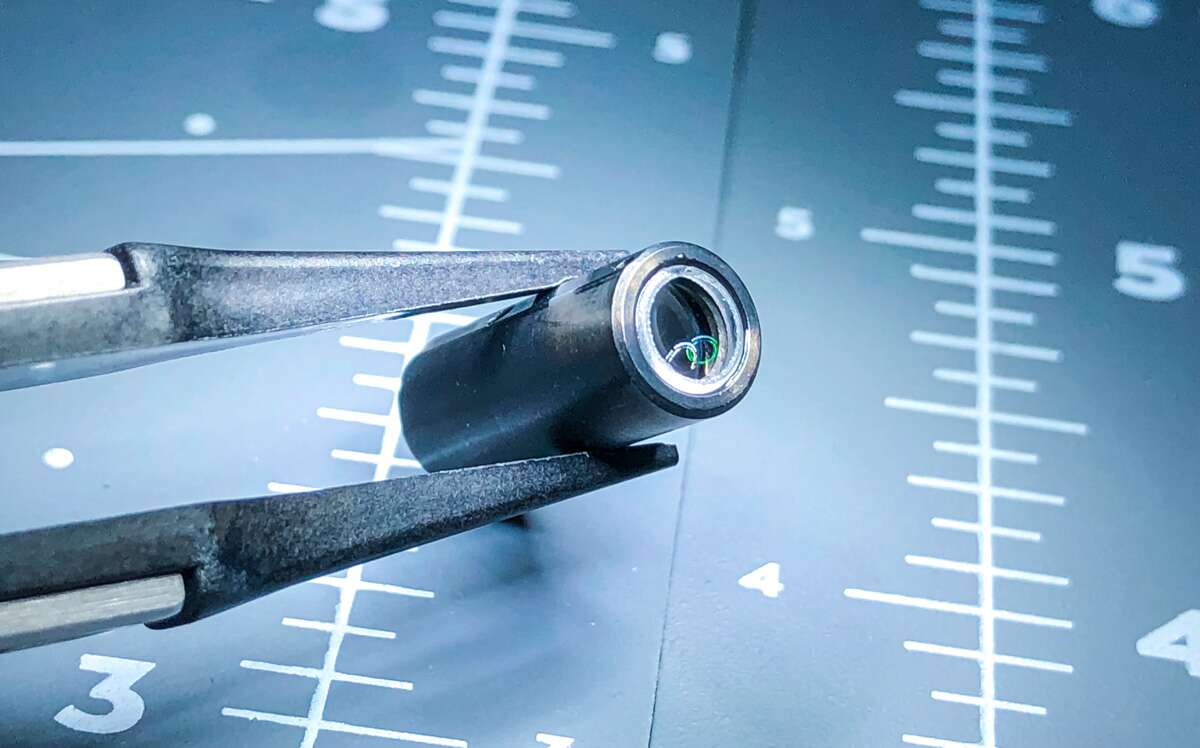
Please do not leave this page until complete. This can take a few moments.
In 2020, Gray Optics saw a surge in demand from manufacturers of COVID-19 point-of-care tests.
Founded in 2017, the Portland company develops advanced imaging technologies and optical systems for biomedical, life sciences and industrial applications.
With the pandemic, manufacturers of point-of-care tests, which provide disease detection and diagnosis within minutes, asked founder Daniel Gray and his team to design custom optical systems that are an integral part of the tests.
The challenge? Many rapid tests rely on fluorescence detection using a lens that must be precisely aligned, with regard to specifications such as field-of-view and depth-of-field, to a digital image sensor.
“The presence of COVID can be detected through fluorescence imaging: In simple terms, does the sample glow a specific color or not?” says Gray.
The COVID sample goes through an assay, a process for analyzing a sample, that uses a mixture of chemicals and compounds that include fluorescence labels.
“The result can be read by an optical system,” he says. “The technology uses light sources, cameras and filters.”
When it comes to manufacturing, optical systems may not immediately come to mind. But companies in the imaging space deal with complex assemblies of components and ever-evolving innovations that put them on the forefront of the manufacturing sector.
As at Gray’s firm, the pandemic has highlighted the industry’s essential role in manufacturing, not only in the medical field but also for life science, industrial and other markets.
Maine has a growing cluster of companies in the imaging space, although it remains a relatively small field. Typically, folks who are involved in visualization are called optical engineers; the companies deal with the engineering aspects of light and bring together components such as lenses, illumination, camera sensors, software and electronics.
“In its most basic form, optical imaging is the process of collecting light and recording and displaying that information in a way that’s useful to humans,” says Tom Snyder, CEO of Lighthouse Imaging in Windham. “In a sense, it can act as a remote eye to allow vision where it would not otherwise be possible.”
Optical imaging provides the ability to capture and store images and video for later use.
“A typical optical image system will utilize a series of lenses to focus an illuminated scene on an image sensor and create a digital representation of that scene” — something as common as a picture on a computer monitor, Snyder says.
Gray Optics supports medical, life sciences, 3D printing and industrial markets. In the medical space, that includes developing surgical robotic systems, retinal imaging, dental cameras — anything that uses a camera to take pictures of people. For life sciences, optical technologies are used for diagnostics or analytical applications such as tissues and blood sample specimens. In 3D printing, lasers, mirrors and lenses are critical.
Industrial markets use similar technologies for inspecting mechanical systems.
“For example, an aircraft engine has thousands of parts,” says Gray. “You don’t want to take it apart to inspect it, so having a flexible inspection camera, or borescope, to do inspections is valuable.”
A typical product development project came from a startup in Boston that’s innovating visualization for minimally invasive surgery, using an endoscope that’s inserted into a port within the body.
“They’re providing the surgeon with pictures of the anatomy that can’t normally be seen with their own eyes,” says Gray.
Gray’s team worked on the lens design, using the basic functional product requirements the Boston company had developed through its prototypes.
“We did the commercial product design for them, paying attention to things like manufacturing tolerances, material choices and the assembly process,” he says.
On a simpler level, optical imaging encompasses everyday things like binoculars and laptop cameras, notes Dennis Leiner, founder of Leiner Optics in Cape Elizabeth and vice president of the Bioscience Association of Maine. Leiner founded Lighthouse Imaging in 1984 and sold it in 2010. His new company assists startups and Fortune 500 companies that are incorporating visualization into their medical devices.
A typical optical system used in medicine, he says, is the endoscope, which might have as many as 30 lenses to relay light from the tip of the narrow instrument within the body out to a camera. Some newer systems have a tiny camera right at the tip.
Visualization is the primary link between surgeons and their work. Parameters to consider include physical size, overall image quality, illumination requirements, working distance, field of view, direction of view, optical resolution and sterilization techniques, says Snyder.
Cost is also important.
“If the cost does not align with our customer’s business model, we don’t have a viable commercial product,” Snyder says.
For example, Lighthouse develops 2D and 3D camera systems that integrate with surgical robots. Stereoscopic 3D systems require precise alignment of two lenses and two image sensors to mimic eyeballs.
“The camera is made up of a number of different optical elements, or lenses,” he says. “It has electronics and electronic interconnects that transmit the image signal from the image sensor back to our central processing unit. We design and utilize precision mechanical components and housings that create the structure for the optical and electronic components.”
Hand-assembly of the tiny components, measuring as little as one millimeter cubed, requires excellent hand-eye coordination while working under a microscope, Snyder says.
“This takes place in a very clean environment,” he adds. “Any dust or debris in the optical path will create a blemish on the image itself.”
Lighthouse designs, prototypes and manufacturers sub assemblies and full imaging systems. Prototype development typically involves design tweaks based on client feedback. A common tweak, for example, is tuning that addresses image quality.
“It could be the colors aren’t quite accurate,” says Snyder. “We can tweak the color palette of the image. That’s common.”
Going from concept to manufacturing can take 12 to 24 months. Initial prototyping takes four to eight weeks, depending on factors such as complexity of the device and use of off-the-shelf versus custom components.
A component that’s evolved considerably over the years — shrinking in size while gaining in resolution — is the image sensor.
“The typical sensor we use today is 1 millimeter by 1 millimeter,” or four-hundredths of an inch square, Snyder says. “That enables us to reduce the overall size of the device, which reduces the entrance size required to penetrate into the human body and minimizes the impact to the patient.”
Leiner says much of that improvement has to do with the shrinking of components that go into cellphone technology.
In Scarborough, Yokogawa Fluid Imaging Technologies Inc. offers a “value add” to optical technology. Its flow imaging technology, called the FlowCam, combines digital imaging, microscopes and flow cytometers — which analyze microscopic cells or particles suspended in a liquid medium — into a single instrument. New artificial intelligence software expands the instrument’s image-analysis capability.
The instruments are used in fields such as marine research, municipal water management and industries ranging from biopharmaceuticals and chemicals to oil and gas. The instrument can be used to study the amount and type of toxic algae in drinking water reservoirs and the correct formulation of therapeutic drugs.
“A lot of our instruments are generally the same and applied to different applications,” says CEO Kent Peterson.
When developing new products, design parameters include magnification, illumination, imaging frequency, flow rates and size of the glass channel that’s appropriate for specific samples, he explains. There’s the nature of the sample — is it toxic, hot, pressurized? Software specifications might need to account for contrast between particles and the medium they’re in.
“Are you looking at, say, a translucent particle in drinking water? You need to have software specifications that can pick out that image,” he says.
The company sources components from other companies and assembles them at its Scarborough facility, where it also writes the computer programs that analyze the samples.
“We keep an eye on other technologies to incorporate into ours,” says Peterson. “We’re almost blessed because our components are sourced from other companies, and that’s their core competency. So we cherry-pick the best, the newest, the smallest, the fastest of the cameras or microscope objectives or lasers. While they’re improving their products, we’re the beneficiaries, incorporating it into the FlowCam and making the FlowCam a better product.”
The FlowCam is being used to develop COVID-19 vaccines at Pfizer, Moderna and other pharmaceutical companies, says Peterson.
“The FlowCam is used in part in that development process,” he says. “It’s also used in the development of therapeutic drugs for treatment. And we’re supplying instruments to companies making PCR [diagnostic] tests for COVID.”
As a result, 2020 resulted in the company’s strongest year. Expected for 2021 is continued growth and a planned 50% workforce increase, from 30 employees now to 45 by the end of the year.
Faced with aggressive product development schedules due to the health emergency, Gray Optics also grew, doubling its staff in 2020. Now it’s planning for continued growth in staff and facility space in 2021.
“We are forecasting further growth in the company and making plans to continue to hire local talent and planning investments to expand our manufacturing to support the needs of our customers,” says Gray.
Lighthouse Imaging, too, has seen increased demand for the medical imaging devices it designs and manufactures, such as those used in airway management. Snyder notes that the pandemic also highlighted the risk of cross-contamination between patients, resulting in greater demand for single-use devices.
“Our growing team here has shown great dedication and pride in supporting COVID patients around the world,” says Snyder.
Leiner predicts further growth in the field in Maine.
“It’s a pretty hot industry,” he says. “I wouldn’t be surprised to see people moving to Maine to start their own company.”
At the same time, he adds, being part of a niche field is pretty special.
“We all know each other in Maine and even across the country and around the world,” says Leiner. “One takeaway I have about visualization companies in Maine is how collegial it is. It’s the opposite of cutthroat, which is very nice. It’s typical Maine.”
0 Comments