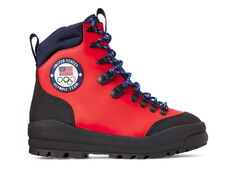
Please do not leave this page until complete. This can take a few moments.
The US athletes at the Paris 2024 Olympic and Paralympic Games wore Ralph Lauren jeans and jackets during the opening and closing ceremonies.
What’s of local interest is that two family-owned Maine manufacturers played a significant role in the creation of Team USA’s fashion presence.
Rancourt, of Lewiston, produced the buck white suede shoes. Rogue Industries, of Standish, manufactured the belts.
“We’re proud to support local American manufacturing in the development of Ralph Lauren’s parade uniforms to bring unique specialties and distinctly American perspectives to the table,” says Tom Hunter, the corporate communications lead for Ralph Lauren, which has been the official outfitter for the U.S. Olympics and Paralympics since 2008.
Ralph Lauren engages a range of local vendors and partners to source high-quality fabrics and technologies from the U.S. to develop the Team USA uniforms.
This year, it partnered for the fourth time with Rancourt to manufacture the shoes for the US athletes. It was the first time Ralph Lauren partnered with Rogue Industries.
“Rogue Industries and Rancourt are examples of family-owned operations in Maine that have a reputation in producing incredibly high-quality goods,” says Hunter. “In engaging local manufacturers for the belt and shoes for the 2024 uniforms, Rancourt and Rogue Industries’ “Made in Maine’ focus, and their commitment to incredible quality made them both a natural fit as two of the partners contributing to Ralph Lauren’s Team USA uniforms.”
Before Team USA athletes could walk in the white suede shoes, their journey began at a factory in Lewison, which has a long history of shoemaking.
The Rancourt family has been crafting moccasins for three generations, going back to 1967. Mike Rancourt has led the company with his son Kyle since 2009. Rancourt produced shoes worn in Olympic games in Brazil, Tokyo and Beijing.
“Ralph Lauren was our first customer for Rancourt & Co. in 2009,” says Rancourt. “I had a close contact at Ralph Lauren and they weren’t happy with the supplier they were using in the United States and they asked if I would be willing to do business with them. For our first Olympics, we made red, white and blue boat shoes.”
In 2023, Ralph Lauren asked Rancourt to come up with a new design, which is how the manufacturer came up with a white buck suede shoe. All of the shoes are handmade in the Lewiston factory.
“From a quality-control point of view, it is as rigid as you’ll find in the shoe business and so extraordinarily demanding,” says Rancourt. “Ralph Lauren has an expectation system … Anytime you start a new product — if you are a maker, it doesn’t matter what you make — your first production on new products is where you’re really learning.
“We didn’t have a lot of room for error,” he continues. “But once you get through that, everyone starts to learn the nuances of different raw materials and different aspects of the shoe style they are making.”
For this year’s shoe, the Ralph Lauren design was based on Rancourt’s style, the “classic buck shoe.”
“They send us a detailed sheet of the style itself,” says Rancourt. “It is the raw material with the leather, lining, souls, stitching thread, and fit points they want us to work with. It requires a lot of work, and it took us two months to get all the pieces put together. Finally, they do a fit trial. They will take something we are making and fit it on two or three individuals at the company. Once the design is approved, we begin placing orders for the different products.”
In the interim, the company had 30 employees working on the shoes.
Rancourt says the company made 200 to 300 shoes weekly. He says they were in production for the Olympic shoes for six months.
Rancourt says it is challenging for the factory to make Olympic shoes. He says that if Ralph Lauren reaches out for the 2026 Winter Olympics — which will be held in Milan and Cortina d’Ampezzo, Italy — he won’t refuse it. But if it doesn’t happen, he is OK with that.
“We have been really pleased and are apt to do it. It brings a lot of pride to our workforce and the city of Lewiston,” says Rancourt. “It is important from that perspective.”
Rogue Industries, a family-owned Standish business known for its leather goods, was established in 2007 by Michael Lyons.
Like many companies, Rogue grew out of a common issue. The founder was unhappy with his bulky back pocket wallet, which he was convinced was causing his back pain. He set out to learn about leather and design. Now, the company sells its products to large companies, including L.L.Bean.
Lyons says the connection with Ralph Lauren started with a talk with another Maine manufacturer, Portland-based Sea Bags.
Sea Bags “was kind enough to refer Ralph Lauren to us,” Lyons says.
He said the process began with a formal application, which entailed a substantial capabilities audit.
Once informed it had won the contract, it was full steam ahead for Rogue’s nine-person team, which had just months to tackle the project.
Rogue and Ralph Lauren collaborated on a military-style belt made from webbing with a buckle design. “It all starts with a design,” Lyons said.
From there, he said it’s about sourcing components such as leather, cotton weaving, jacquard lettering, thread and custom metal buckles.
The biggest challenge was identifying and locating U.S. suppliers within the limited time frame. Potential suppliers had to be thoroughly vetted for quality and production capability.
“A project like this involves so many pieces that it was essential that we had time to identify and work with our suppliers before going into production,” says Lyons. “With every single piece needing to be sourced exclusively here in the U.S., we knew that it would entail a substantial amount of supplier vetting.”
Many component samples and finished prototypes were sourced and tested. Some suppliers provided a single component, like the buckle, while others brought a sub-assembly of webbing and jacquard.
“We had some excellent production partners along the way that clearly understood this was not a standard production run,” says Lyons. “This program happened because our employees and contract suppliers all leaned into the effort together.”
With the Olympics now a memory, Lyons reflects on the experience.
“This program took an extraordinary amount of effort and time. But how often does a Maine company of nine people get an opportunity like this? There were only eight suppliers from the entire United States which participated in this,” Lyons says. “Would we do it again? We would certainly have to look at the opportunity very closely.”
The Giving Guide helps nonprofits have the opportunity to showcase and differentiate their organizations so that businesses better understand how they can contribute to a nonprofit’s mission and work.
Learn MoreWork for ME is a workforce development tool to help Maine’s employers target Maine’s emerging workforce. Work for ME highlights each industry, its impact on Maine’s economy, the jobs available to entry-level workers, the training and education needed to get a career started.
Learn MoreWhether you’re a developer, financer, architect, or industry enthusiast, Groundbreaking Maine is crafted to be your go-to source for valuable insights in Maine’s real estate and construction community.
Coming June 2025
Learn moreThe Giving Guide helps nonprofits have the opportunity to showcase and differentiate their organizations so that businesses better understand how they can contribute to a nonprofit’s mission and work.
Work for ME is a workforce development tool to help Maine’s employers target Maine’s emerging workforce. Work for ME highlights each industry, its impact on Maine’s economy, the jobs available to entry-level workers, the training and education needed to get a career started.
Whether you’re a developer, financer, architect, or industry enthusiast, Groundbreaking Maine is crafted to be your go-to source for valuable insights in Maine’s real estate and construction community.
Coming June 2025
In order to use this feature, we need some information from you. You can also login or register for a free account.
By clicking submit you are agreeing to our cookie usage and Privacy Policy
Already have an account? Login
Already have an account? Login
Want to create an account? Register
In order to use this feature, we need some information from you. You can also login or register for a free account.
By clicking submit you are agreeing to our cookie usage and Privacy Policy
Already have an account? Login
Already have an account? Login
Want to create an account? Register
This website uses cookies to ensure you get the best experience on our website. Our privacy policy
To ensure the best experience on our website, articles cannot be read without allowing cookies. Please allow cookies to continue reading. Our privacy policy
0 Comments