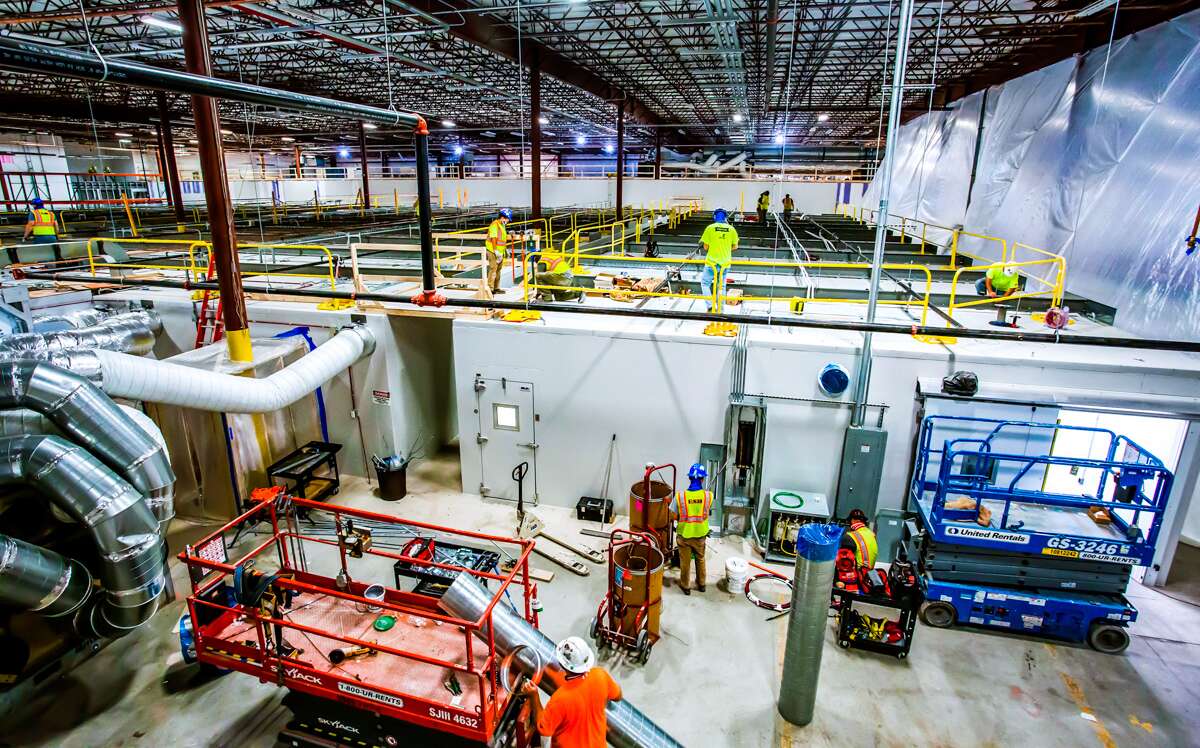
Please do not leave this page until complete. This can take a few moments.
Kevin French sits in a cramped conference room in a Westbrook industrial building and tries to capture the previous two months.
“What we’ve done here is something I’ve never heard of, never been part of before,” says the vice president of Landry/French Construction.
To the layperson, the 126,072-square-foot building at 5 Bradley Drive is just one of many big industrial boxes in the 5 Star Industrial Park.
To French, it’s the embodiment of the defining project of his company’s 10-year history.
It’s July 9, the day after the Scarborough-based construction company was issued a certificate of occupancy for the building it is renovating for Abbott Laboratories (NYSE: ABT), a Chicago-based company with sales of $31.9 billion last year.
Abbott, which has a site in Scarborough, is expanding production of its rapid COVID-19 tests, and needs the production space. It leased the building this spring from Calare Properties LLC, which bought it for $8.75 million.
When French got a call in late April from Abbott saying they wanted him to look at a building they were thinking of fitting out, French was happy to comply. The construction firm, celebrating its 10th anniversary this summer, and Abbott go way back. Abbott was Landry/French’s first customer, and they’re currently also partnering on an expansion on Abbott’s Scarborough campus.
French took a look at the building, which had been an Olympia Sports distribution center. It had a maze of conveyor belts and was set up for distribution, not for producing diagnostic devices.
French says dismantling that type of building and fitting it out for the kind of production Abbott does takes a year or more. This one had to be done in two months.
On May 8, the day after Calare closed, Landry/French was on site.
Everything had to come out. “We needed a shell to work with,” French says. “We were going to have to build from scratch.”
That involved taking down the tangle of conveyor belts then building half a dozen smaller buildings inside the building, adding climate control and overhauling the infrastructure — Abbott needs three times the power load that the building was fitted for.
The construction firm, which employs 50, also had 13 or 14 other jobs going on.
And, of course, it was all happening during a pandemic. “Everyone told me it was impossible,” says French. That just fueled his resolve.
To hit that deadline, everything had to go right. Everyone involved had to not only be on top of their game, but also on top of new games they’ve never played before. Here’s a look at how that worked.
“Many people, when they found out what we were doing said, ‘You’re kidding,’ I’d say, ‘No, we’re not kidding, we’re going to do it,’” French says.
But others were willing to jump on board. Craig Piper, a principal at SMRT Architects and Engineers, got a call on a Saturday night about the project. By Wednesday, SMRT was on site. That’s not how it usually works.
“We have a process,” Piper says. They take a look, talk to developers, come up with some designs, and meet in a couple of weeks. “Nothing really changes the process.”
This project did. Piper and his team, who have worked with Landry/French many times, didn’t flinch. They were at 5 Bradley Drive that first week, and someone has been there every day since.
That attitude was shared among the team, up to 150 to 160 workers on site some days.
“All the trades rallied to support this project,” French says. “They knew what was at stake and they wanted to be part of it.”
While the management is from Landry/French, a number of subcontractors work on any job. “Everyone worked together,” French says. “It didn’t matter what the hard hat said, we were all on the same team.”
One benefit of the pandemic was that because some developer put projects on hold, “we were able to get the best people,” French says. “I feel like I’m surrounded with the A Team, and it made my job a lot easier.”
Piper says it also meant pairing the right people, and making sure the right architect or engineer was on site the same day the subcontractor or other person from a different team who they needed to work with — aligning people’s schedules to things worked efficiently.
Decisions were made on the fly in ways neither Piper nor French had ever seen before. Piper says holding back rather than giving a wrong answer went out the window. “Here, any answer was better than no answer,” he says.
People from Abbott were also on site, so decisions could be made quickly. “We’d huddle and make decisions on the fly,” says French.
Decisions that usually took weeks, or even months, were done in an hour, or a day. “We had to stay on schedule,” he says. “A miss would be big. There was no wiggle room.”
Piper says preparing a massive empty space for an intricate production process is complicated, with a lot of moving pieces.
Normally, they’d put together three, four, five designs for something. “Here we had one and had to go with it,” he says. “Early decisions had to stick.”
That could be unnerving. “I never had so many wake-up-in-the-middle-of-the-night moments as I did with this, wondering if I’d made the right decisions,” Piper says.
When Landry/French first came onsite, five or six workers were methodically dismantling the conveyor belts, a process that can take weeks.
French’s team took over and deployed 52 welders, cutters, people to unbolt things and do other jobs, and 10 pieces of heavy machinery. The belts were down in five days. That set the tone.
There’s usually one supervisor overseeing a job site, but Landry/French used five, one for each trade.
When it was discovered the floor was an inch and a half out of level, Piper’s design team scrambled to make new designs, a process that normally would have taken months.
“It was remarkable,” says French. “I’ve never seen anything like that.”
That was part of the new architectural process. Architects usually spend most of their time at their office, but Piper’s team was right there, designing.
“We’d do a sketch at 5 p.m. and at 6 a.m. the next morning they’d be building it,” he says.
When it was clear the massive climate control machinery wasn’t going to arrive on time, they leased machines, which will be removed when the purchased ones arrive.
Normally, the Maine Turnpike does not permit wide loads on summer weekends, but when a load of 80-foot trusses were on their way up on Memorial Day weekend, Peter Mills, director of the Maine Turnpike Authority, gave the OK for the trucks to proceed.
French says Mills, in a state police car, met the trucks at the New Hampshire border and escorted them to Westbrook.
When they arrived on Bradley Drive, workers took them right off the trucks and installed them that day.
While some big projects with a tight deadline might operate around the clock, French says people do better and safer work if they get some rest.
“You can run a jobsite around the clock and have 200 people and be 50% effective, but you wanted to be 100% effective from day one,” he says. They had 12-hour shifts, and never wavered from that game plan.
“It proved true,” he says. With more than 100,000 hours of work there were no injuries.
“I never saw anyone let their guard down,” he says.
That went for COVID-19 safety too. Precautions included mask-wearing, hand-washing stations, temperature checks and more. The company had a small outbreak at its Scarborough project site, but not in Westbrook.
Despite his certainty that it could be done, French says, “There were a few nights I went home and said, ‘What did I get myself into?’”
But the day he talked to Mainebiz, he could relax. The certificate of occupancy came the afternoon before, two months to the day after Landry/French arrived at 5 Bradley Drive.
The construction team was finally able to unpack and install equipment that had to wait for the certificate. A few rooms down, dozens of Abbott trainees were having their first session.
There’s still a second phase of the project left to do, but Landry/French hit its deadline and Abbott will shortly be producing more rapid COVID-19 tests.
As the pandemic ramped up and the need for tests increased, the pressure grew. But French says those involved were also energized by the fact they were part of the effort to combat the pandemic.
“They saw the big picture,” he says.
Piper says he can’t think of anything he’d do differently. French, though he’s still processing, can’t either.
A week before, the company that he’d founded with Denis Landry had marked its 10th anniversary.
French says they look back with pride at every project they build. They’ve had some notable ones, most recently the Bill and Joan Alfond Commons, in Waterville, which has won awards and is already a landmark on the city’s Main Street.
But the Abbott project, inside a big box of a building among a lot of other nondescript boxes, is special. He says it’s testament to the company’s staff, and the team, which stayed focused on what had to be done.
“This is a career-defining project for us,” French says. “It gave us self-confidence and showed what we can accomplish.
“I was confident we could do it. I never doubted we could do it.”
0 Comments