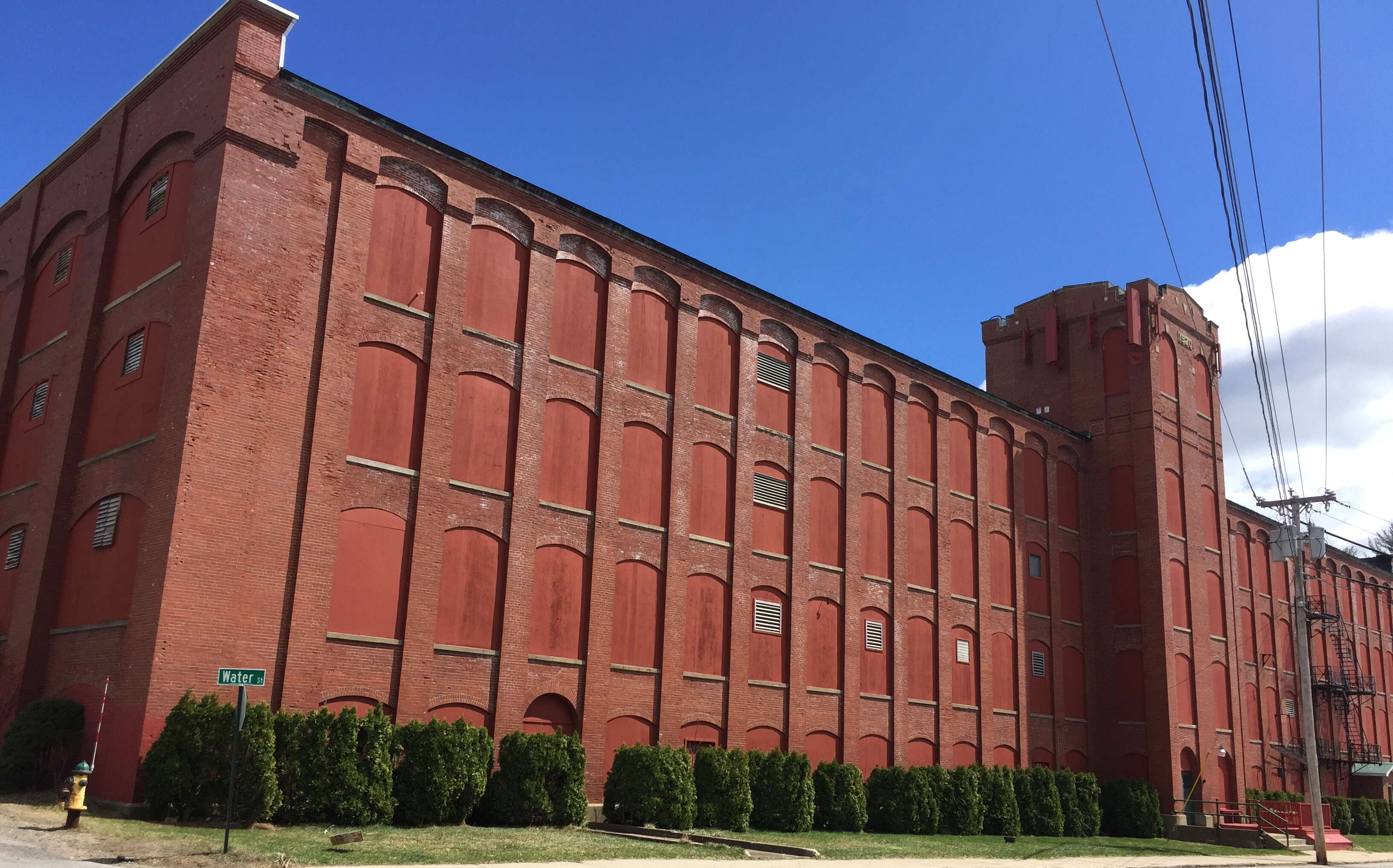
Please do not leave this page until complete. This can take a few moments.
A spinning company with Maine roots dating back over a century sold its Springvale mill and warehouse to a New Hampshire developer, but holds a leaseback for continued operation.
Chinburg Properties bought 5 Water St. from Jagger Brothers LLC for $1.3 million. Cheri Bonawitz and Karen Rich of Malone Commercial Brokers represented the buyer and Suzanne McKechnie of Investcomm Commercial Group represented the seller.
The property has two industrial buildings totaling 68,000 square feet on 2.87 acres.
“My family has been in the town for a long time,” said David Jagger, the seller and the owner of Jagger Spun, a maker of worsted spun yarns. “It was very important to me that the property be sold to somebody who would have a positive impact on Springvale and I’m convinced that they’re the ideal company and that Eric is the ideal person to do that.”
Jagger continues to operate his yarn-spinning business, Jagger Spun, in a portion of the building.
The York County property was marketed as a well-maintained building in great working condition.
One building is an 8,800-square-foot partially heated warehouse with three overhead doors and a loading dock that’s operating as an office and warehouse. The other building is a former spinning mill and retail shop totaling 60,000 square feet on four stories.
All floors are equipped with bathrooms and heat. The building is fully sprinkled and has brick walls, hardwood floors and a cargo elevator.
“We had solid interest from several well established developers,” said McKechnie. “I am pleased to see this iconic property will continue to be part of the community and being developed for a sustainable purpose. I believe its future is in great hands.”
The worsted spun yarn operation started in southern Maine with the arrival of Uriah Jagger and his family from England in the 1880s. Uriah was a yarn spinner and had obtained employment with Goodall-Sanford Mills in Sanford.
Uriah’s sons, Samuel and Fred, incorporated as Jagger Brothers in 1906 and continued operation sat a South Sanford location until 1956, when the company moved to the neighboring town of Springvale.
Sam’s sons — Allan, Winston and Robert — purchased 5 Water St. and moved operations there.
In the late 1980s, Allan’s son, David, started Jagger Spun as a separate division to provide quality yarn for production weavers and knitters. In 2014, Jagger Spun was expanded to include retail customers worldwide.
In 2019, David closed the Jagger Brothers operation but kept open the Jagger Spun division, continuing to operate at the Water Street location with a small workforce.
Jagger Spun manufactures “worsted spun” yarns. The difference between worsted and woolen spun yarns is in the preparation, according to the company’s website.
The fibers in worsted spun yarn are combed to be parallel and uniform before spinning, whereas the fiber for woolen spun yarns are more casually arranged. Because the fibers are parallel, worsted spun yarns are denser and less airy than woolen spun. Woolen spun yarns bloom more after washing and are lighter and airier. Worsted spun yarns are smoother and have better stitch definition. They are also stronger, more durable and less prone to pilling.
As a kid, Jagger used to visit the Sanford mill that Sam and Fred initially operated.
“It was like visiting Willy Wonka’s chocolate factory,” he said. “It had a water wheel and all these belts that went two stories up and would drive the shafts that went the length of the building.”
The next generation — David’s father Allan and Allan’s brothers Robert and Winston — bought the mill in Springvale. David has a photo of the mill from when it still had a belfry on top. He later donated the bell to the Springvale Public Library.
Jagger Spun was started as a specialty division for custom orders, he said. Niche items include wool/silk blends and “heather” yarn, which blends different shades.
“We were the funny little company in Maine that could do unusual things,” he said.
Development firm Chinburg Properties, of Newmarket, N.H., is owned and led by Eric Chinburg, who has over 30 years of experience saving and restoring mill buildings in Maine, New Hampshire, Massachusetts and Vermont.
Chinburg said he and his team are always on the lookout for new opportunities.
“The Jagger Mill was being marketed for sale and came to our attention through Cheri Bonawitz at Malone Commercial Brokers,” he said.
He continued, “We are very excited about the opportunity to create another special project at Jagger Mill. It is an excellent example of why we love saving historic buildings: its brick and beam construction, large factory style windows and high ceilings simply cannot be replicated with new construction.”
He noted the mill is also located in the center of Springvale, within easy walking distance to local businesses and recreation areas.
Financing for the acquisition was secured with Machias Savings Bank.
Plans for the property?
“We are looking to adaptively reuse the property into approximately 90 apartment homes while also preserving the building’s architectural and industrial character,” Chinburg said. “Any future project would be utilizing state and federal historic tax credits, which are critical to project feasibility and ensure the highest standard of historic preservation as overseen and administered by the National Park Service.:
To convert the building into housing, he added, Chinburg Properties will make “significant” investment in the property including all new windows, new building systems and new utilities, as well as significant site improvements including new storm water infrastructure and landscaping.
Said Jagger, “I’m so pleased it’s going to become housing. I couldn’t be happier.”
The Giving Guide helps nonprofits have the opportunity to showcase and differentiate their organizations so that businesses better understand how they can contribute to a nonprofit’s mission and work.
Learn MoreWork for ME is a workforce development tool to help Maine’s employers target Maine’s emerging workforce. Work for ME highlights each industry, its impact on Maine’s economy, the jobs available to entry-level workers, the training and education needed to get a career started.
Learn MoreWhether you’re a developer, financer, architect, or industry enthusiast, Groundbreaking Maine is crafted to be your go-to source for valuable insights in Maine’s real estate and construction community.
Coming June 2025
Learn moreThe Giving Guide helps nonprofits have the opportunity to showcase and differentiate their organizations so that businesses better understand how they can contribute to a nonprofit’s mission and work.
Work for ME is a workforce development tool to help Maine’s employers target Maine’s emerging workforce. Work for ME highlights each industry, its impact on Maine’s economy, the jobs available to entry-level workers, the training and education needed to get a career started.
Whether you’re a developer, financer, architect, or industry enthusiast, Groundbreaking Maine is crafted to be your go-to source for valuable insights in Maine’s real estate and construction community.
Coming June 2025
In order to use this feature, we need some information from you. You can also login or register for a free account.
By clicking submit you are agreeing to our cookie usage and Privacy Policy
Already have an account? Login
Already have an account? Login
Want to create an account? Register
In order to use this feature, we need some information from you. You can also login or register for a free account.
By clicking submit you are agreeing to our cookie usage and Privacy Policy
Already have an account? Login
Already have an account? Login
Want to create an account? Register
This website uses cookies to ensure you get the best experience on our website. Our privacy policy
To ensure the best experience on our website, articles cannot be read without allowing cookies. Please allow cookies to continue reading. Our privacy policy
0 Comments